- Huyett Marketing Department
- 04/18/2024
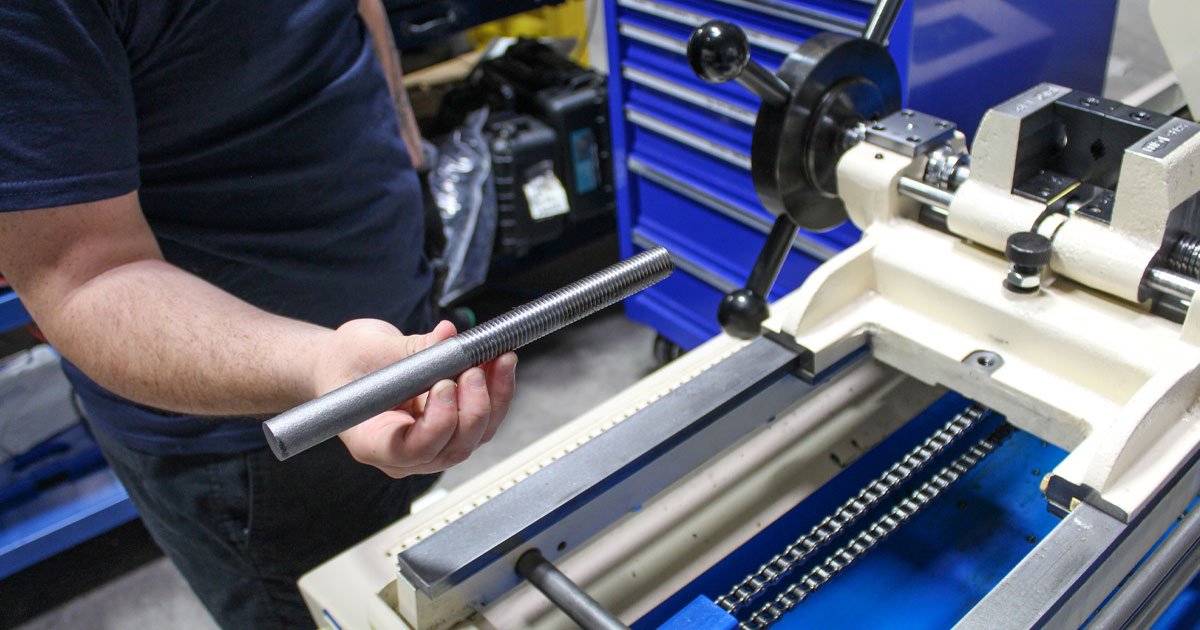
In the manufacturing world, threads are installed onto
rods,
studs, shanks, and into bores in a variety of ways, all of which depend on the design of the component or fastener. Material, thread placement and design, and application needs will all come into play when these threads are created.
At a high level, there are two distinct ways to thread a part: cutting and forming, both of which are offered through
Huyett’s manufacturing processes. Each of these categories use different individual techniques, tools, and machinery, but it is important to first understand how each technique is unique.
Cutting vs. Forming Threads
These two threading techniques are differentiated based on how they manipulate the fastener material.
- Thread Cutting: The process of removing material from the fastener to cut the desired thread shape; popular methods include turning, tapping, and milling.
- Thread Forming: The process of displacing the fastener material by pressing or rolling it into shape; popular methods include tapping and rolling.
Thread Cutting
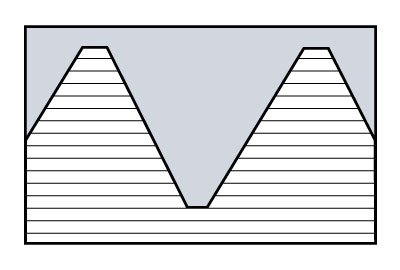
Cutting provides several advantages as a manufacturing process. For example, it is cost-effective for smaller volumes and efficient because one milling tool can make multiple thread sizes. It also allows for versatile cuts, as both turning and milling can cut threads with single or multipoint tools. Additionally, cutting is preferred when the material is too hard to form, as it may be too brittle to be reshaped without breaking. However, cut threads are not as strong as formed threads because the material grains are disturbed and interrupted; the process also creates scrap waste.
Turning
Turning is a process that uses a lathe to cut either internal or external threads. The thread cutting tool (which can be single or multipoint) remains stationary against the workpiece while the workpiece spins at high speeds. This works well with uniquely shaped fasteners and when high tolerances are required.
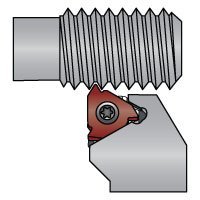
Tapping
Tapping is a process used to make internal threads, both in cutting and forming. Cut taps tend to feature flutes or grooves to allow for metal shavings to exit the hole as it is tapped. This method allows for tapping in material that is not conducive to forming, like hard metals or even plastics. It also works better when the hole is large, as it requires less force than forming.
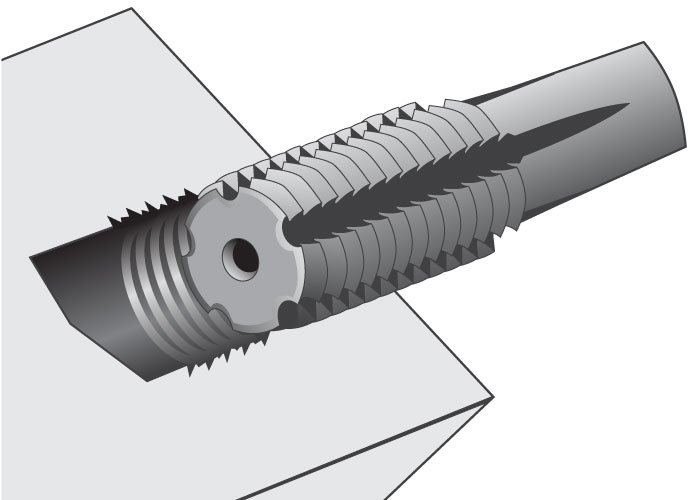
Milling
The milling process is opposite from turning, in that the cutting tool either rotates around (for external threads) or within (for internal threads) a stationary workpiece to cut threads. One of the main benefits of this technique is that one tool can create different sized threads, increasing its versatility and expanding the customization options for threaded fasteners. Milling also facilitates more precise threading, better control of flying debris, and shorter machining time.
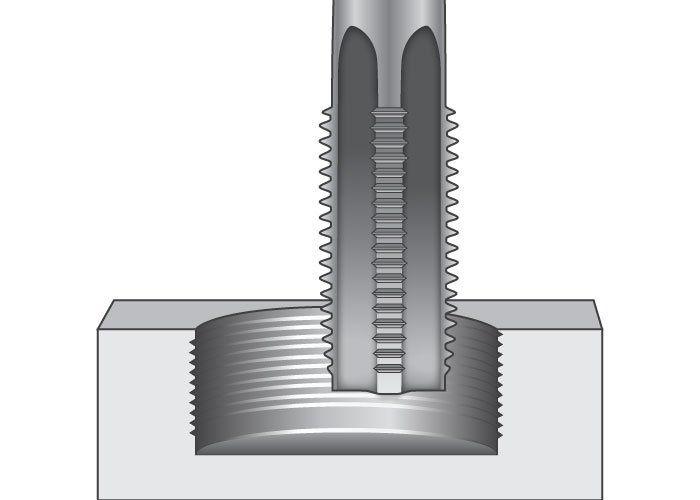
Thread Forming
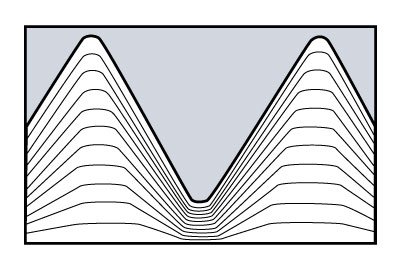
Forming is a more complex process. Since the material is pressed or rolled, it must be worked at the proper temperature, which requires time management. The fastener size must also be considered; since the material is not removed, the displacement will increase major diameter. However, it is cost-effective in high-production and large-volume runs, provides additional cost savings on blanks (since you can start with a smaller diameter), and forms a much stronger thread because it does not cut the grain flow. It also eliminates scrap waste.
Tapping
Tapping, as mentioned above, is the term used to describe internal thread creation. Form taps, also called roll taps, rotate within a workpiece and move the metal into position. Because the metal is displaced rather than removed, the tapped hole’s major diameter will be slightly bigger than a cut hole as the metal is pushed.
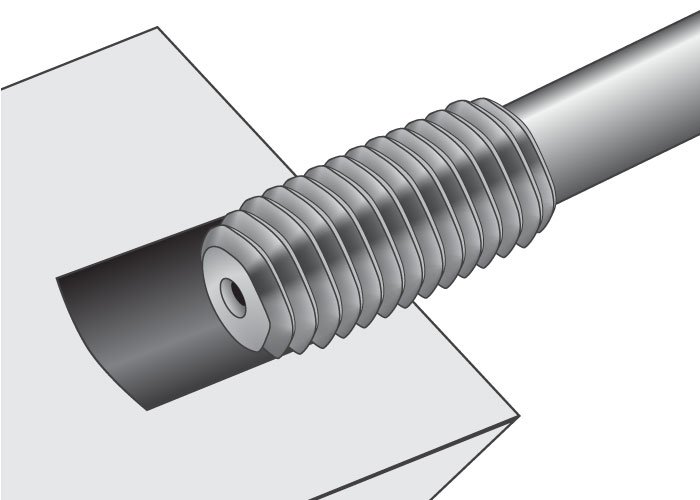
Rolling
Rolling is the method used to form external threads on rods, studs, and fastener shanks. The workpiece is placed between two dies in a thread rolling machine; one die stays stationary while the other rolls against the workpiece, forcing it to conform to the shape of the dies. This is a quick and efficient process, but it is important to know how the diameter of the workpiece will increase during forming so you can begin with an appropriately sized blank.
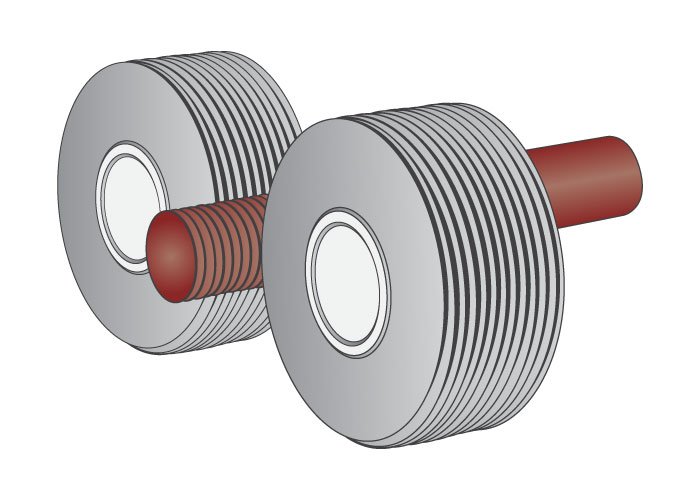