- Huyett Marketing Department
- 12/09/2021
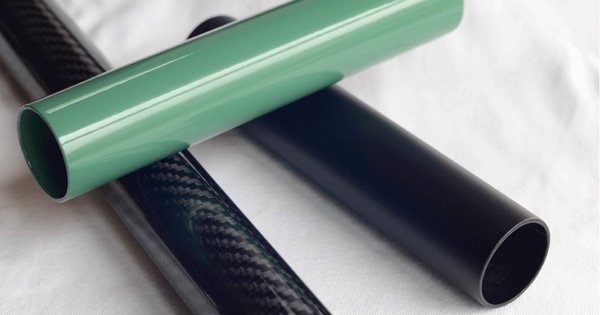
Finishing is the final process in the manufacturing of many metal parts. Finishing makes parts look good, but it also protects them from corrosion, extending their shelf life and reducing maintenance. Painting and powder coating are two of the most widely used finishing techniques.
Both finishes coat the part in a layer that keeps moisture and oxygen from the substrate; however, they are made of different ingredients and applied using different processes. Each has strengths and weaknesses that impact its suitability for particular applications.
What is Powder Coating?
Powder coating is a dry finishing process. A powder is electrostatically applied to a surface and heated. The powder melts and flows together to form a thick, durable finish.
The powder is made of polymer resins, pigments, leveling agents, flow modifiers, and other ingredients. These are melted, mixed, and allowed to cool and solidify. The solid is then ground into a powder ready for application.
Powder coating is often applied through electrostatic spray deposition, although there are other techniques. First, the part is thoroughly cleaned to remove oils, moisture, and other contaminants. Then, the powder is applied via a spray gun. While it travels through the spray gun, it is given an electrostatic (negative) charge. The part to be coated is grounded, so the charged powder is attracted to it. The powder sticks to the part, quickly forming an even layer.
The parts are moved to a curing oven, where heat melts the powder. It flows together and reacts chemically to form molecular chains, providing a hard, durable protective coating.
While spraying is a widely used powder coating technique, parts can also be powder coated by fluidized bed coating. Fluidization forces air through a bed of powder, causing it to behave like a liquid or gas. The parts are heated and then dipped into the fluidized powder, causing the powder to melt and adhere to the part.
What is Painting?
In contrast to powder coating, paint is a liquid mixture of ingredients that typically include pigments, solvents, and binders. Pigments provide the color, and binders hold the pigments together and help them to form a film on an object's surface. The solvent is a liquid — often oil or water‑based — that allows the paint to be applied more easily. As the solvent evaporates, the paint forms a hard layer.
Paint can be applied with brushes, but in industrial scenarios, it is almost always applied with a pneumatic spray gun. Spraying is faster, more efficient, and can be automated on high‑volume production lines. Additionally, spraying provides an even and uniform coating with a superior finish.
Powder Coating: Pros and Cons
Powder Coating Pros
- Powder coating creates a thick, hard finish that is more durable than most painting finishes. It is more resistant to chips, scratches, and wear than paint.
- Powder coat is typically applied as a single layer, although multiple layers are used in some scenarios. This contrasts with paint which often requires multiple coats.
- Powder coating creates an even finish across parts, providing excellent protection for complex shapes.
- Unlike paint, powder coating does not rely on solvents, which are harmful to worker health and the environment.
- Powder coats retain their color longer than most paint finishes.
- Powder overspray can be collected and reused, resulting in significantly less material loss than painting.
Powder Coating Cons
- Powder coating tends to produce thicker finishes. It may be possible to create thin powder coat finishes, but it is more complex and often produces an undesirably rough surface.
- Powder coating requires special equipment, including an electrostatic booth and a curing oven.
- Powder coating is more expensive than painting.
Some Materials Cannot Be Powder Coated
Powder coating applied by electrostatic deposition is best suited to metals. Metals can be grounded, which is essential to attracting the electrostatically charged powder. Metals are also better able to endure the high temperatures required for curing.
Non‑conductive parts can be powder coated, but not electrostatically. The powder would just fall on the floor. To powder coat materials such as plastic, glass, or wood, they must first be heated so that the powder melts on contact and sticks to the surface.
Neither powder coating technique is suitable for materials that are damaged by heating, including many plastics.
Will Powder Coat Rust?
Powder coating does not rust, and it is excellent at protecting metal surfaces from rusting. Powder coat finishes resist peeling, cracking, chipping, and chemical exposure. Provided the coating is not damaged and has been applied to an appropriately prepared substrate, the underlying metal is safe from corrosion — improperly prepared substrates may cause flaking, bubbling, and peeling. However, no finish is indestructible even when it is applied correctly, and damage may allow water and moisture to penetrate. Once rust begins to form, it may spread and damage the finish in adjacent areas.
How Durable Is Powder Coat?
Powder coat finishes are more durable than painted finishes. Powder coating can protect metal for as long as two decades. However, exposure to moisture, UV, and heat degrades both finishes over time in a process called chalking. Chalking occurs at different rates depending on the environment the part is exposed to. An outdoor environment causes faster chalking, particularly if the part is in direct sunlight or exposed to harsh weather.
The quality of the powder and paint used also impacts their life cycle. More expensive UV‑resistant paints and powders retain their color and protective capabilities for longer than less durable alternatives.
Painting: Pros and Cons
Painting Pros
- Painting does not require high temperatures to cure, making it ideal for parts made of plastic and other materials that would be damaged during the powder coat curing process.
- Paint offers a broader range of colors, and it's easier to mix colors to a customer's specifications.
- Paint can provide a thinner finish than powder coating.
- Painting has lower setup and production costs than powder coating.
Painting Cons
- Paint is less durable than powder coating.
- Paint requires multiple layers to ensure complete coverage and an even finish.
- It is challenging to apply paint with a consistent thickness.
- Paint contains solvents and other harmful substances, making it more challenging to work with and more expensive to dispose of.
Is Powder Coating Better Than Paint?
Powder coating and painting offer similar benefits. They protect parts from corrosion and damage while providing an aesthetically pleasing finish. As we've discussed, each has advantages and disadvantages. Which is "best" depends on the requirements of the project.
Powder coating generally provides a thicker, more damage‑resistant finish that needs less maintenance than painted finishes. It is, however, more expensive, and it is not appropriate for parts that require thin finishes. On the other hand, paint is sufficiently durable for many applications, components can easily be repainted in the field, and painting is inexpensive compared to powder coating.
Finish thickness in the U.S. is measured in "mils," which are equivalent to a thousandth of an inch or about 0.025 mm. Powder coating thickness varies depending on the application, but between 2.5 and 3 mils is a typical minimum, rising to 6 mils and more for applications that require additional protection. Paint's thickness varies with the type of paint and the number of coats, but between 1 and 2 mils per coat is a reasonable estimate. If thinner finishes are desired, galvanization or conversion coating may be a better option, as discussed below.
Before choosing a powder‑coated finish or a painted finish for your parts, consider the durability, appearance, maintenance, thickness tolerances, and cost requirements on a case‑by‑case basis.
Powder Coat Alternatives
Painting and powder coating are popular finishes for metal parts, but there are many other finishes worth considering. They include:
- Zinc finishes: Zinc is a corrosion‑resistant metal often used to finish steel and other parts. There are various types of zinc finish, including hot‑dip galvanization, mechanical galvanization, and zinc electroplating.
- Conversion coatings: Conversion coating creates a very thin finish formed by chemical or electrochemical threatment. Popular conversion coatings include black oxide, clear zinc, phosphate, and aluminum chromate. Conversion coatings are often used for finishing aluminum, zinc, and copper parts.
- Anodization: Aluminum is anodized by immersing it in an acid electrolyte and applying a direct current. The surface oxidizes and forms a durable corrosion‑resistant eluminum oxide coating. The coating can be colored before a final sealing process.
Huyett manufactures and stocks a wide variety of parts available in many different finishes, including:
- Nuts, Bolts, and Screws
- Washers
- Shaft Retention Components
- Pins and Wire Forms
- Key Stock and Machine Keys
We offer a comprehensive range of secondary processes to help customers achieve their part finishing objectives, including painting, powder coating, conversion coating, galvanization, and more. Learn more about Huyett finishing processes in our
guide to secondary processes or
contact our expert Sales Team.