- Huyett Marketing Department
- 05/02/2024
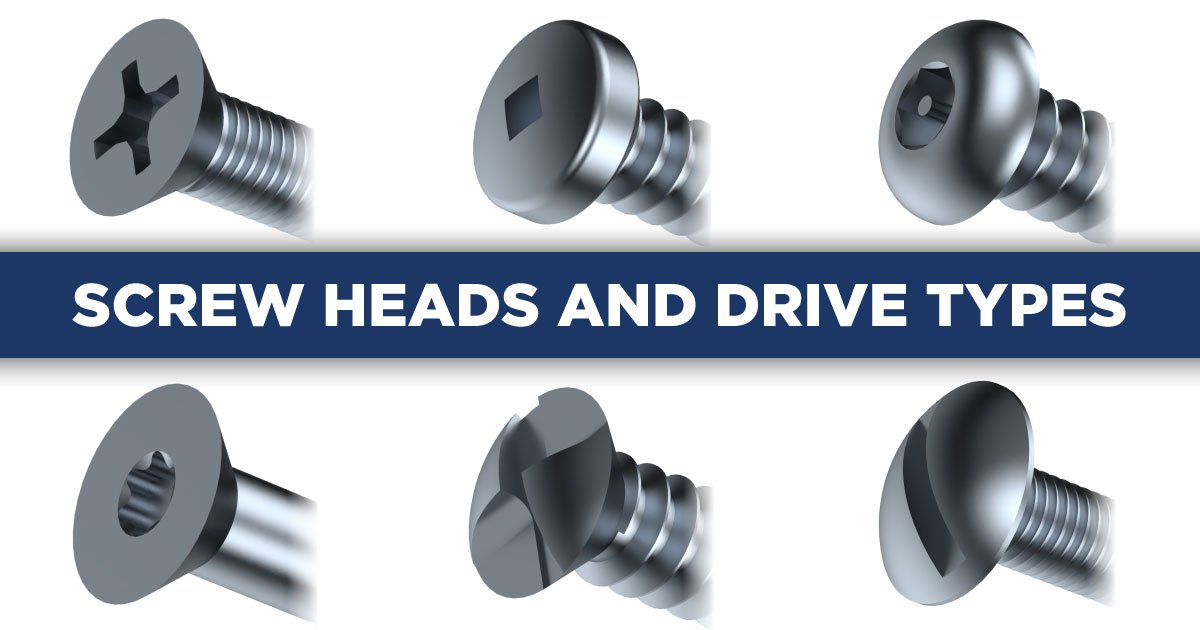
In the world of threaded fasteners,
screws are some of the simplest yet most essential components in use. Offering the basic function of being driven into mating surfaces to form a secure attachment, these affordable fasteners are heavily used in just about any industry – from agriculture to construction to precision food and medical machinery – as reliable connectors. Their versatility is even more expanded by the interchangeability of two specific characteristics: screw head and drive types.
Screw heads and drives come in a wide range of styles, most of which can be combined with each other to offer unique benefits like flush finishes, stronger holds, tamper resistance, and better load distribution. Here, we will focus on the varying styles of these two crucial elements. But first, we’ll review the basic screw anatomy.
Basic Screw Anatomy
Different kinds of screws will always feature their own unique characteristics, but all of them will share this fundamental structure:
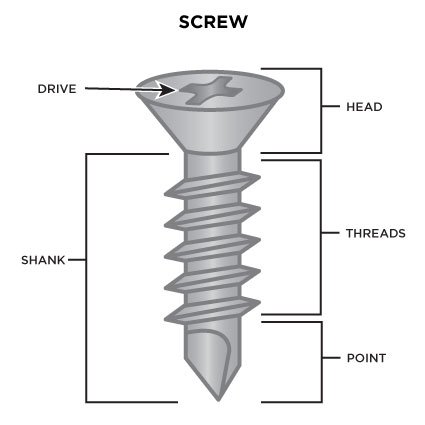
Most of these elements are available in multiple styles. For example, there is a wide range of thread types to choose from that equip screws with different kinds of holding power (often dependent on the mating material), as well as a variety of points and shanks that affect driving capability. This guide will focus on the top of the screw:
Screw Head: The section at the top of a screw extending to the base of the body that houses the drive; this also includes any features on the underhead.
Screw Drive: The shaped element within the head that accepts the tool that will tighten the screw; typically, this is a recessed (or female) shape that accepts a specific type of screwdriver or bit, but some screws have a raised (or male) drive that accepts a socket wrench.
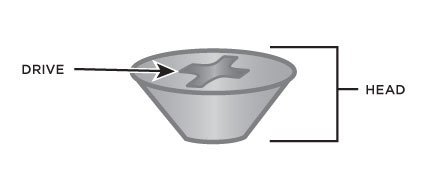
Screw Head Types
The screw head is a defining feature of the entire fastener and often impacts the overall choice, since different styles are designed to offer benefits based on mating materials, load requirements, environment, and other application elements. With a variety of available options, it is important to understand what the different types of screw heads are, how they perform, and what they offer.
Before delving into specific styles, there are two main divisions of screw head types that most shapes fall into: countersunk and non-countersunk.
Countersunk vs. Non-Countersunk
Each type of screw head will, at its most basic level, either be countersunk or non-countersunk:
- Countersunk: Features a tapered underhead that allows it to be driven deeper into the surface.
- Non-Countersunk: Does not feature a taper; the underhead is flat.
This typically means that countersunk screws will sit flush with the surface while non-countersunk screws will protrude above it. However, that is not the
definition
. The taper is the important factor; both styles can feature head types that protrude or sit flush.
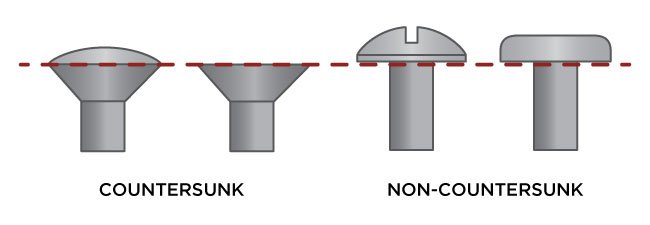
Most types of screws are non-countersunk. For those that are countersunk, there are three head profiles that commonly accompany this style:
Standard:
The taper descends from a standard-size head at an 82° (inch), 90° (metric), or 100° (not as common) angle and directly meets the screw body.
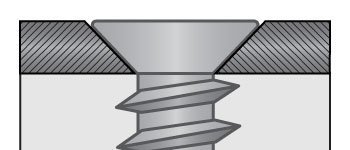
Trimmed:
The taper descends at a standard angle but from a narrower head; these usually have a square drive.
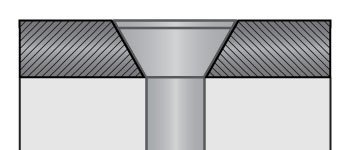
Undercut:
The taper descends at a standard angle from a standard-size head, but meets a flat bottom that sits on top of the screw body.
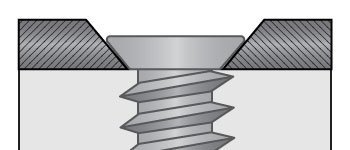
Common Screw Head Shapes
There are many different, more specific screw head shapes that sit atop the screw body. As mentioned above, most of them have flat under heads, but a few of them are tapered. The following list is not extensive; however, it covers the most common head types you’re likely to encounter.
*The chart below is available to download here:
Common Screw Head Shapes Chart
Name
| Description
| Common Uses
| Image
|
---|---|---|---|
Binder
| Thick, cylindrical flat head with a slightly rounded top and a deep drive
| Electrical applications – underhead allows for wire space
| ![]() |
Bugle
| Countersunk with a curved taper and flat top
| Soft materials like drywall and wood – helps prevent splitting and provides a flush finish
| ![]() |
Button
| Low profile, slightly rounded head with a flat top
| Furniture, appliances, equipment assemblies, etc. – used where low profiles are needed
| ![]() |
Cap
| Tall, flat head that looks like a cap with a recessed socket drive
| Sleek designs where there is limited space for external sockets or wrenches – facilitates high-torque installation
| ![]() |
Cheese
| Tall, cylindrical head with no angles and a flat top
| Metal, automotive lighting, machinery, etc. - used where deep drives are helpful; for example, in applications that are often taken apart and reassembled
| ![]() |
Fillister
| Similar to the binder head but with a taller round top
| Replacement screws for older applications or where head height is required – good for low torque applications
| ![]() |
Flat
| Countersunk with straight standard angles and a flat head
| Applications that require flush finishes for minimal interference
| ![]() |
Flat Undercut
| Similar to flat but with a a flat, undercut base
| Light-duty applications like door hinges – works well when a more shallow drive is needed
| ![]() |
Hex
| Six-sided flat head, sometimes indented
| Industrial equipment and construction applications, often in thin materials
| ![]() |
Hex Flange
| Similar to the hex head but with a washer-like flange at the base
| Where larger bearing surface is needed to protect mating surface and distribute the load
| ![]() |
Oval
| Countersunk with a straight angle and a slightly curved top
| Decorative finishes where greater driving force is needed
| ![]() |
Pan
| Short sides with slightly rounded top; the most common head style
| A wide range of applications that require a flat underside
| ![]() |
Round
| Rounded head with no vertical sides
| Where smooth and decorative finish is helpful – not for high-speed use
| ![]() |
Thumb
| Varied design, but all of them feature wide heads that are easy to grip with fingers
| In light-duty settings where hand-tightening is convenient, like control panels or electronic components.
| ![]() |
Truss
| Similar to a round head but with a shorter top and a wider base
| Where a low-profile decorative finish is required – provides a larger bearing surface
| ![]() |
Modified Truss
| Similar to a truss head but with a wider, washer-like base
| In settings like the standard truss but where a lower profile is necessary
| ![]() |
Wafer
| Countersunk and similar to a bugle head but with a wider, washer-like flat top
| Soft materials that need to resist splitting but also require a larger bearing surface
| ![]() |
Screw Drive Types
The
screw drive determines the type of installation tool that is required to tighten a screw. It also facilitates different levels of torque and enables secure tightening in varying materials.
There are a wide range of drives in use today. It wasn’t always that way – screws used to only feature slots and square heads until the Industrial Revolution. This brought on the need for drives that could withstand high-production environments, which meant they needed to exhibit better cam-out resistance and be compatible with industrial tools.
Screw manufacturers took this opportunity to patent their own screw drives and matching tools to offer unique benefits that spoke to specific industrial needs. As successful drives began to emerge, manufacturers then developed their own versions of these designs. This is largely why, today, we have multiple versions of similar drive types.
Now, there are a few distinct characteristics that can apply to several drive types: whether they are male/female, combined, or tamper resistant.
Male and Female Drives
Drives are split into male and female types:
- Male: Drives that are a protruding or raised head (no internal drive) and require a wrench or similar took for installation, like a hex head.
- Female: Drives with an internal slot or shape that require screwdrivers or bits for installation, like a slotted or Phillips® shape (makes up the majority of screws).
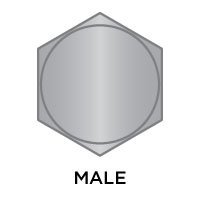
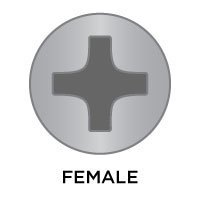
Male-drive screws are often identified as bolts. Technically, this does not define the difference between a bolt and a screw. A bolt is a fastener that requires a nut during assembly, while a screw does not, regardless of the drive. However, since most bolts are male and most screws are female, Huyett identifies bolts as fasteners that do not feature internal drives, while those that do have internal drives are screws.
Combination Drives

This drive, as the name suggests, combines different drive types on one head. The main combination is Phillips and slotted. There are others, but they are much less common.
Tamper Resistant Drives
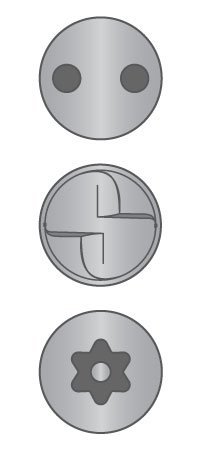
These drives feature unique shapes that only work with specific installation tools, which is what makes them tamper resistant. For example, a slotted drive screw is easy to remove and therefore are not meant to provide this security; even if you do not have a flathead screwdriver, these can be loosened with a knife or other flat component. Drives with unique characteristics – like snake eyes or pins – are not accessible by average tools.
These screws are often used in components that are exposed but require security to prevent theft or loosening, like bathroom stalls, boats, public transportation, public benches, libraries, etc.
Common Screw Drive Shapes
While the following table does not list every existing drive style, it is inclusive of most common shapes.
*The chart below is available to download here:
Common Screw Drives Shapes Chart
Name
| Description
| Common Uses
| Image
|
---|---|---|---|
Combination Slotted Phillips
| Features a full slot and a Phillips recess, allowing it to be installed with either respective drive tool
| In any setting where either a slotted or Phillips drive is appropriate or where the choice is convenient
| ![]() |
Hex
| Six-sided protruding head, common in bolts
| Widely used in many applications, including in construction and machinery
| ![]() |
External Slotted
| Slot within a protruding hex
| A wide range of light-duty and existing applications
| ![]() |
External Square
| Four-sided protruding head with no internal drive
| Where frequent manual adjustments are required – the square head is easy to grip with wrenches
| ![]() |
Hex Socket
| Internal six-sided recess that requires a
hex key for installation
| Industrial and electronic applications – somewhat tamper resistant as they are less common
| ![]() |
Hex Socket with Pin
| Internal hex recess with a protruding pin in the middle; tamper resistant
| Where some degree of security is necessary, like public property or items that may pose a risk if loosened
| ![]() |
One Way
| Unique, curved shape with a slot extending one way
| Where some degree of security is necessary – slotted screwdrivers will install it but it needs special removal tools
| ![]() |
Phillips
| A rounded cross-shaped recess
| A wide range of applications where installation slippage is a particular concern
| ![]() |
Phillips Square Driv with ACR®
| A standard Phillips drive but with additional cam-out ribs on opposite ends of the cross (these mate with respective bits to provide extra grip)
| Applications that require additional installation grip with no increased force from the installer
| ![]() |
6-Lobe
| A six-pointed star recess
| Where cam-out resistance during installation is especially necessary
| ![]() |
Six Lobe with Pin
| A standard 6-lobe recess with an additional pin protruding from the middle of the recess
| Where a degree of tamper resistance and cam-out resistance are necessary
| ![]() |
Slotted
| A single slot across the entire screw head
| In a wide range of light-duty applications that require easy-to-find installation tools
| ![]() |
Square
| A square-shaped recess
| General applications that require additional cam-out resistance
| ![]() |
U-Drive
| A smooth, rounded head
| Where aesthetic finishes and a degree of tamper resistance is needed
| ![]() |
As you can see, screw head and drive types are essential design elements to consider when choosing screws. It is important to evaluate the application’s environment, requirements, and materials before deciding which type of screw will best support those specific needs.
If you have any questions, feel free to reach out to our friendly
Sales Team for more information on Huyett’s product selection.