- Huyett Marketing Department
- 12/02/2020
Corrosion is the gradual degradation or destruction of materials (usually metals) by electrochemical reaction with its environment. In the case of metals, it is the process of rusting — oxidation in reaction to oxygen forming iron oxides. It requires the simultaneous presence of water and oxygen and in the absence of either corrosion does not occur.
The process of steel corrosion occurs in stages. Initially, corrosion begins at anodic areas on the surface where ferrous ions go into solution. Electrons are released from the anodic surface site and travel through the metallic structure to adjacent cathodic sites where they combine with oygen and water to form hydroxyl ions. These react with the ferrous ions from the anodic site to produce ferrous hydroxide, which itself is further oxidized in air to produce hydrated ferric oxide (rust). The chemical process can be represented with this equation:
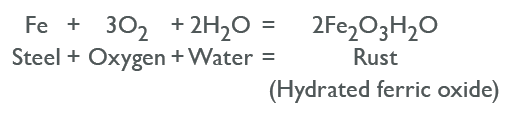
After a period of time, accumulation of rust on the surface can cause the corrosion process to be suppressed. New anodic sites may form in adjacent areas allowing further corrosion. In this case, over long periods of time, the loss of metal is reasonably uniform over the surface, and this is usually described as general or uniform corrosion.
Anodic sites release electrons and cathodic sites receive electrons forming the basis of the electrical circuit driving the corrosion process.

Common Forms of Corrosion
Many alloys corrode merely from exposure to moisture in air, but the process can be strongly affected by exposure to other substances. In addition to wide‑area damage, corrosion can be concentrated locally to form a pit or crack. Because corrosion is a diffusion‑controlled process, it occurs on exposed surfaces. As a result, methods to reduce the activity of the exposed surface, such as passivation and chromate conversion, can increase a material's corrosion resistance. However, some corrosion mechanisms are less visible and less predictable.
Uniform Attack Corrosion
Also known as general attack corrosion, this type is the most common and is caused by a chemical or electrochemical reaction that results in the deterioration of the entire exposed surface of a metal. Ultimately, the metal deteriorates to the point of failure.
Uniform attack corrosion accounts for the greatest amount of metal destruction by corrosion, but is considered a safe form of corrosion because it is predictable, manageable, and often preventable.
Intergranular Corrosion
Intergranular corrosion is a chemical or electrochemical attack on the grain boundaries of a metal while the individual grains remain relatively intact. This often occurs due to impurities in the metal, which tend to be present in higher concentrations near grain boundaries, causing the boundaries to be more vulnerable than the bulk of the metal. The alloy eventually loses strength as the grains fall out.
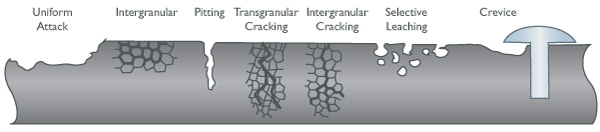
Pitting Corrosion
Pitting results when a small hole or cavity forms in the metal, usually as a result of a small scratch, damage to the protective coating, or some other depassivation of a small area. This area becomes anodic, while part of the remaining metal becomes cathodic, producing a localized reaction. The deterioration of this small area penetrates the metal and can lead to failure. Pitting is often difficult to detect because it is usually relatively small and may be hidden by a layer of rust.
Stress Corrosion Cracking
This form of corrosion is caused by the combination of tensile stress and a corrosive medium. The surface of the structure can remain relatively untouched while fine cracks progress through the interior. These cracks can be intergranular — proceeding along grain boundaries — or transgranular — cutting through individual grains. This type of stress can be disastrous because failure can occur within the design specifications of both stress and corrosion. Hydrogen embrittlement can also cause stress cracks and failure, but its mechanism and treatment is vastly different.
Selective Leaching Corrosion
Also known as dealloying corrosion, this type of corrosion attacks a specific element in an alloy. The most common type of dealloying is dezincification of unstabilized brass resulting in deteriorated and porous copper. Other alloy systems can lose aluminum, iron, cobalt, chromium, and other elements. Rather than describing each with its own label such as dezincification, they are all known as selective leaching.
Crevice Corrosion
Similar to pitting, crevice corrosion occurs in hidden locations such as under gaskets, washers, clamps, bolts, and screws. Acidic conditions or a depletion of oxygen in a crevice can lead to crevice corrosion.
Galvanic Corrosion
Galvanic corrosion, or dissimilar metal corrosion, occurs when two different metals are placed together in a corrosive electrolyte. A galvanic couple forms between the two metals, where one metal becomes the anode and the other the cathode. The anode, or sacrificial metal, corrodes and deteriorates faster than it would alone, while the cathode deteriorates more slowly than it would otherwise. Three conditions must exist for galvanic corrosion to occur: electrochemically dissimilar metals must be present, the metals must be in electrical contact, and the metals must be exposed to an electrolyte.
Flow‑Assisted Corrosion
Flow‑assisted corrosion, or flow‑accelerated corrosion, results when a protective layer of oxide on a metal surface is dissolved or removed by wind or water, exposing the underlying metal to further corrode and deteriorate.
Fretting Corrosion
Fretting corrosion occurs in the form of pits and grooves on the surface as a result of repeated wearing, weight, and/or vibration on an uneven, rough surface. It is often found in rotation and impact machinery, bolted assemblies and bearings, and surfaces exposed to vibration during transportation.
Huyett applies a thin coating of rust inhibitor to all of its machined products to prevent the onset of corrosion.