- Huyett Marketing Department
- 02/15/2021
- Updated: 06/27/2024

Grease is an essential lubricant in many applications. Unlike oil, grease is thick and sticks to the component surface, providing longer-lasting lubrication. However, on its own, it is much harder to control during application. Grease guns provide a clean and controlled application method that moves grease directly from the gun through a grease fitting coupler to a grease fitting, where it is evenly dispersed into the application. Different types of grease guns have unique designs that help facilitate lubrication in a variety of applications, from high-volume manufacturing and commercial equipment to small, custom projects.
What Is a Grease Gun?
A
grease gun is either a manual, battery-operated/electric, or pneumatic tool used to pump grease into an application that needs lubrication, typically ones with moving parts. It is used for precisely applying grease to
grease fittings in various equipment types, ranging from passenger vehicles and lawn equipment to aircraft and aerospace applications. It usually features a cylindrical grease gun barrel to hold a grease cartridge, a trigger or plunger for pumping the grease out of the barrel, and a grease fitting hose, extension pipe, or nozzle.
Grease Gun Types
There are many different designs and types of grease guns, each one suited for specific application needs. For example, manual grease guns - like lever-handle and pistol-grip guns - are easy to use but may not be as conducive to high-volume applications. On the flip side, pneumatic and cordless/electric grease guns are better suited for high-volume setting but tend to be a bigger investment.
The four most common types of grease guns are divided into two categories: manual and automatic. Within the manual category, lever-handle and pistol-grip pistols are the most popular options. As for automatic options, air-powered and battery-powered are the preferred choices.
Types of Manual Grease Guns
Manual grease guns tend to be the more economical choice, partly because they are hand operated and partly because they do not require additional equipment to work. They are ideal for low-volume applications like personal projects/equipment or repairs on older automotives. They are also better suited to applications that require more precise grease disbursement, as the handheld trigger or lever allows the user to control the grease flow.
Lever-Handle Grease Guns
Lever-handle grease guns provide the most volume/stroke. To operate, hold the gun in one hand and pump the lever with the other; this requires more room and “elbow grease” than a pistol-grip gun needs, but it facilitates more lubrication with one pump of the lever. They are well suited for applications with controlled lubrication needs that do not require high-production, repetitive use.
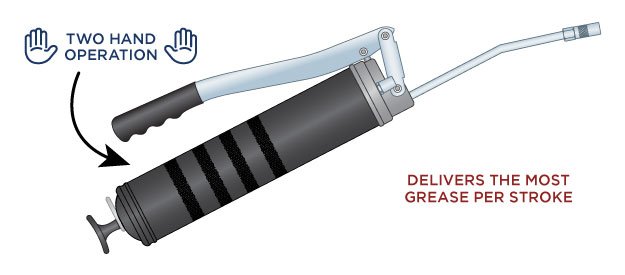
Pistol-Grip Grease Guns
Pistol-grip grease guns offer a more compact solution for tight, awkward, or enclosed spaces. Using just one hand to pull the trigger, these guns require less energy and space to operate. Since the trigger does not provide as much pressure as a lever, pistol-grip options do not disperse as much grease/stroke. Consider this option if the application is low volume, in a small or awkward space, and would require controlled lubrication disbursement.
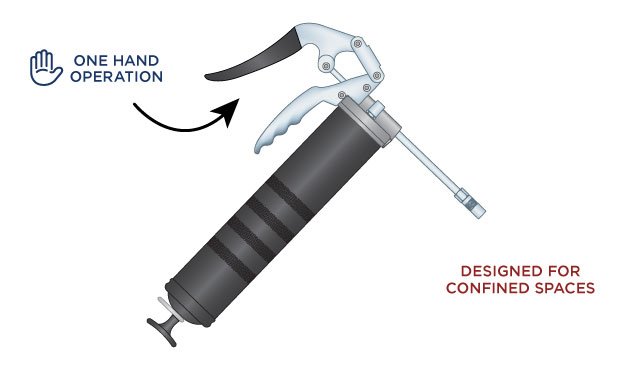
How to Load a Cartridge
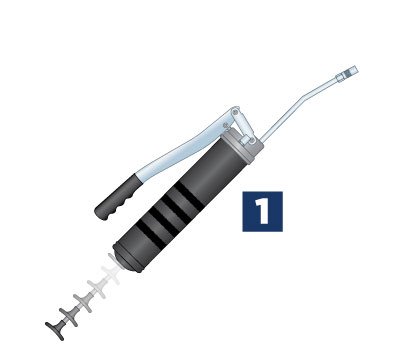
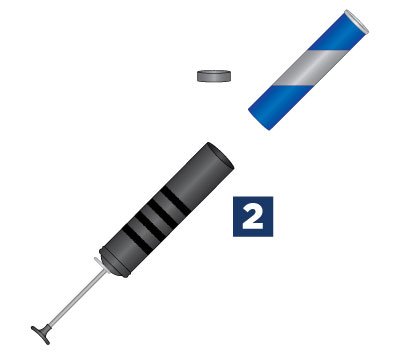
1. Pull plunger back, and lock in place.
This seals to prevent leakage and contamination.
2. Remove plastic cap.
Grease cartridge should be inserted into the gun face down.
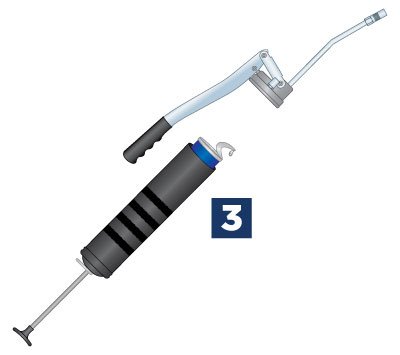
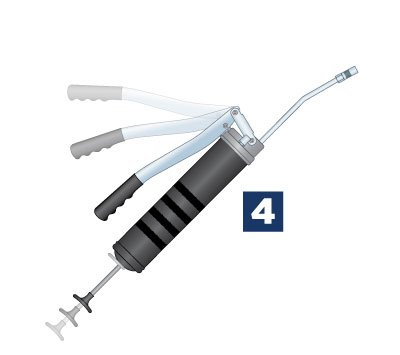
3. Remove flip-top lid on cartridge.
Replace grease gun head.
2. Release plunger lock.
Pump lever several times to prime.
After loading the grease barrel and attaching it to the gun head, the air bleeder valve provides a method for releasing entrapped air from the grease barrel providing easier gun priming.
Types of Automatic Grease Guns
Automatic grease guns facilitate lubrication through an attached source of power. The two most common types of automatic grease guns are air-powered (pneumatic) and battery-powered, each of which provide significant pressure to discharge the grease without taxing the user, who only needs to pull the trigger. While these guns are more expensive and do not control the grease flow like a manual grease gun, they are well suited for high-volume and repetitive lubrication applications and often handle cold temperatures more efficiently than their manual counterparts.
Pneumatic Grease Guns
Pneumatic grease guns use a compressed air supply to deliver a steady, consistent, and high-powered grease flow. Since the pressure is enhanced (even compared to other automatic grease guns), they are well suited to industrial and high-volume applications (they are also effective when paired with bulk loading equipment). It is important for the user to be trained in handling this particular type of grease gun; misuse poses more risk since the gun is powered by compressed air. Considering this, they are more suited for professional work.
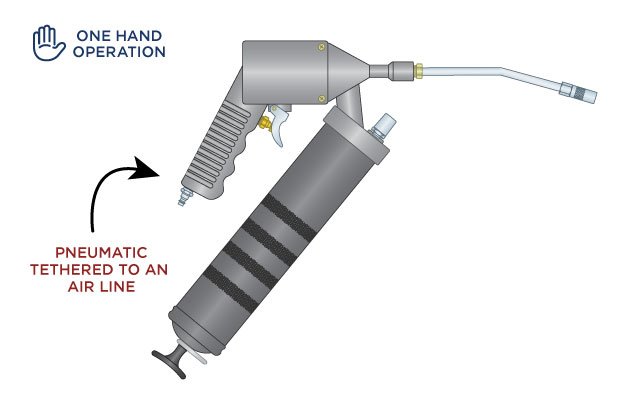
Battery-Powered Grease Guns
Battery-powered grease guns are cordless and use rechargeable batteries to stay portable and easy to use. They deliver grease at a much higher volume and do not require “elbow grease” from the user; this helps prevent the user from tiring during long, high-volume, or repetitive jobs. Since the gun is not manual, it is harder for the user to manage the grease output. However, this is not as important if the application does not require significant lubrication control.
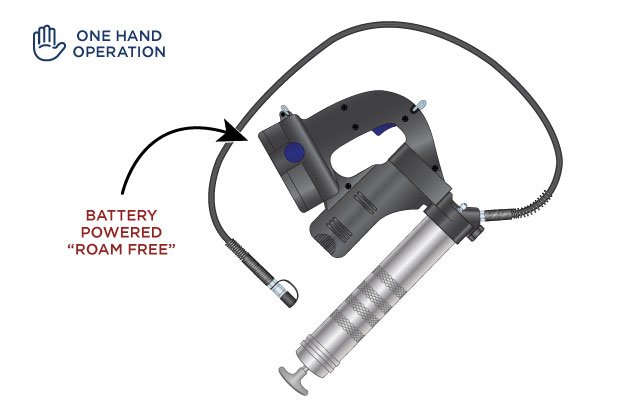
Grease Gun Purchase Considerations
As with any tool, care should be taken in selecting the right grease gun for the application. Over lubricating or using the wrong grease can damage the grease fitting, the gun, or both. Also, the grease itself can be a health concern if allowed to penetrate the skin. Below are some important points to consider when buying a grease gun.
Application
First, define the use. Will the gun be used in commercial, industrial, or custom/small operations? How often will it be used? Does the grease flow need to be controlled? Will the gun need to operate under extreme temperatures? Is it far away from a power source? What kind of equipment will it service?
Pressure
Second, assess the pressure requirements. What pressure is needed to open and dispense grease in the application? High pressure is needed to "unfreeze" clogged fittings with heavy lubricants or in cold weather.
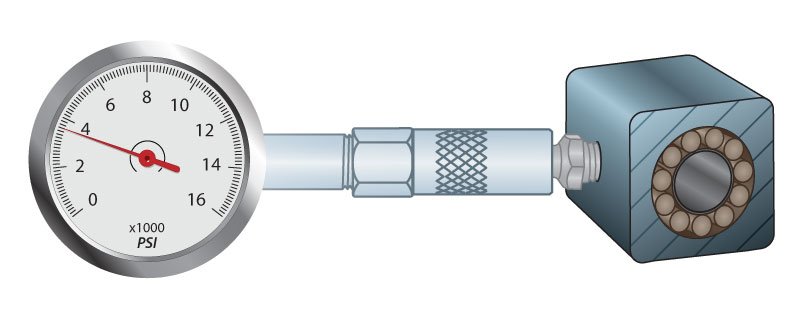
Accessibility
Next, determine space, clearance, and accessibility. Consider awkward angles, reach, tight spaces, etc. The gun must allow a compatible grease gun coupler to access the greasing point and leave enough room to operate it according to its design. The user may want to consider grease fitting hoses, pipe extensions, grease fitting adapters, or
angled grease fitting couplers to increase accessibility to the application.
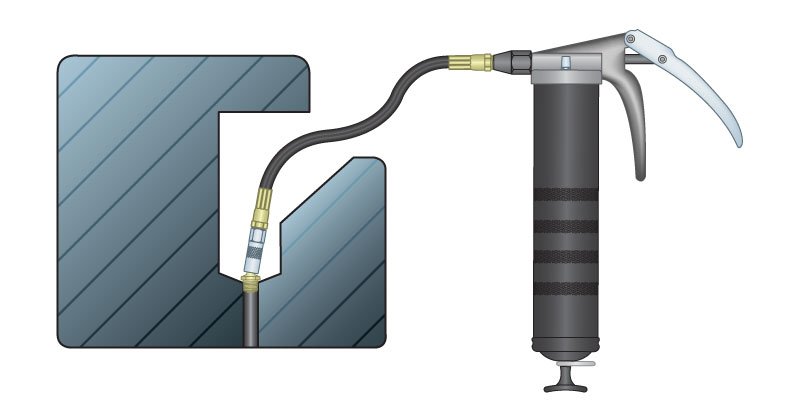
Lubrication
Last but not least, evaluate the type of grease needed for the application. Consider its viscosity, performance under pressure, base makeup, dropping point, etc. This will help the user estimate how it will perform under different application and environmental elements.
Grease Gun Lubricants: What to Consider
Once the user has selected a grease gun, it is important to select the right grease lubricant for the application. The following list, though not exhaustive, points out three key factors to consider when choosing an appropriate lubrication.
- Base Oil Viscosity: Grease is largely made up of oil, which is then supplemented with additives and thickeners. The base oil viscosity (typically between 20-500mm² at 40°C) is the foundation of the overall grease thickness. This is a main factor in determining if the grease is appropriate for the application.
- Additives/Thickeners: Additives fortify the grease with performance-enhancing elements, like antioxidants, rust and corrosion inhibitors, antiwear capabilities, pressure performance capabilities, etc. Thickeners are added to manipulate the grease consistency independently from the base oil viscosity; application speed and temperature are two influential factors in choosing the correct consistency.
- Dropping Point: This signifies the temperature at which grease changes consistency from semi-solid to liquid. It helps identify how hot the grease can get while still maintaining its operational thickness, although that is different than its maximum temperature before it becomes unusable.
Whatever grease is chosen for the application, the most important factor is using it consistently and in accordance with the application requirements.
Grease Gun Accessories
There are several accessories that help increase a gun's reach into the application. The accessories typically help the gun overcome spacing obstacles like tight fits, awkward angles, and hard-to-reach areas. They also make the gun more versatile by allowing it to connect to a variety of different grease fittings.
- Grease Gun Couplers (learn more about these accessories in our Grease Gun Tips and Couplers guide)
- Flexible Grease Hoses
- Adapters and Bushings
- Grease Fitting Tool Parts and Accessories, including (but not limited to):
- Grease Gun Barrels
- Batteries and Chargers
- Gun Holders, Sleeves, and Straps
- Bulk Loader Fittings and Bleeder Valves
How to Use a Grease Gun
To begin with, you will first need to load it (this is covered in detail below). Next, connect the nozzle to a flexible hose or pipe extension, which will funnel the lubrication from the gun into the application. Attach a coupler to the end of the hose or extension and snap it onto an installed grease fittings (
learn how to install grease fittings here) - it should lock into place for a leak-proof seal.
How to Load a Grease Gun
Grease guns are typically loaded in three ways: cartridge, suction, and bulk load. The following section details these methods to help you choose the gun and accessories best suited for your application.
Cartridge Load
The gun is filled using packaged cartridges. These cartridges are convenient but are more costly than bulk loading and can negatively impact the environment because they are single-use.
- Unscrew the canister from the grease gun and pull back the plunger, locking it in place.
- Remove the plastic end cap of the new cartridge and insert into the canister open end first.
- Once inserted, remove the top lid of the cartridge and reattach the canister to the grease gun head.
- Action the pump of the gun until grease flows out of the coupler.
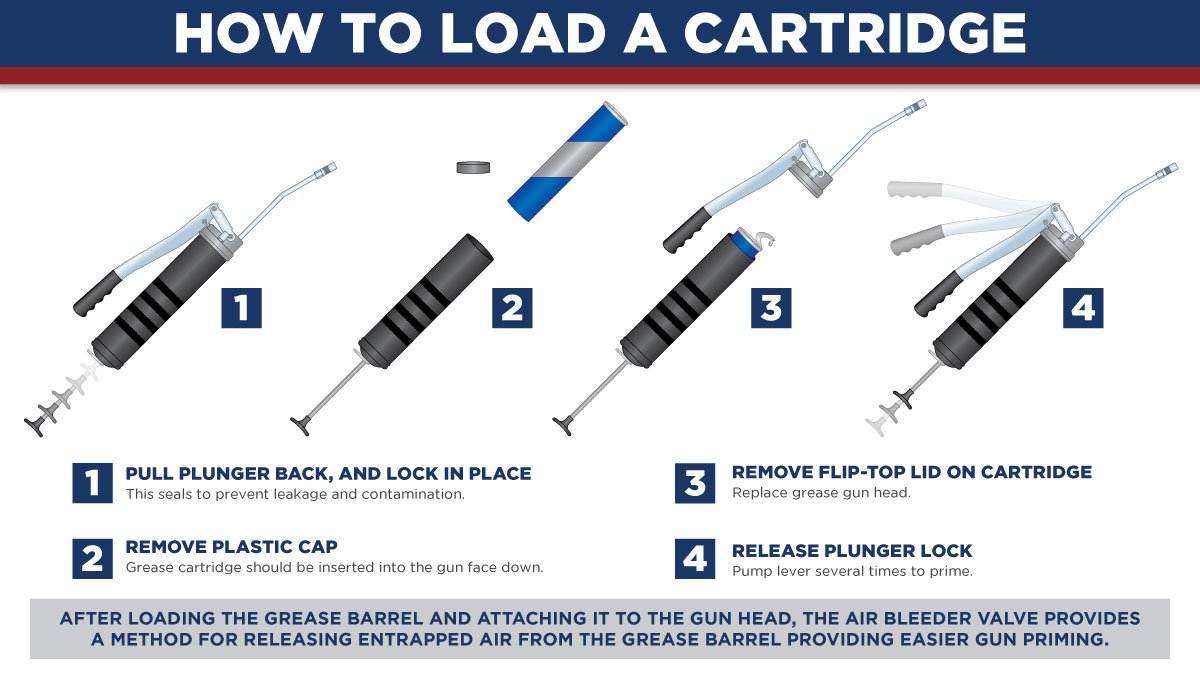
Suction Load
Suction load means the gun is filled manually from a bulk drum by inserting the end of the gun into grease and pulling up on the handle. This method is best suited for lighter grade grease, as it tends to be difficult to extract heavy grease.
- Unscrew the canister from the grease gun.
- Push the open end of the canister into the grease drum so that the end of the canister is completely submerged in grease.
- Grasp the handle of the plunger on the grease gun canister and draw it back to pull grease into the canister.
- Reattach the canister to the grease gun head and push the plunger forward.
- Action the pump of the gun until grease flows out of the coupler.
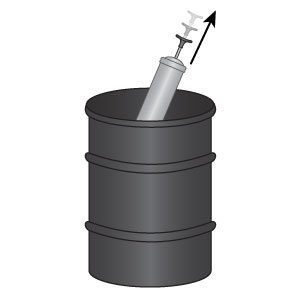
Bulk Load
Bulk loading is the easiest, cleanest, and most cost effective method of reloading a grease gun. Using bulk loading to reload your gun will necessitate purchasing the following items:
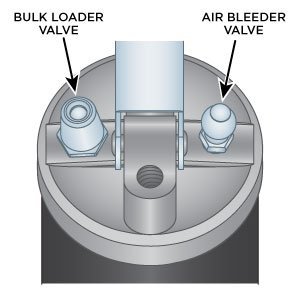
How to Bulk Load
A barrel pump is installed onto a pail or bucket of grease. The gun's loader fitting is pressed onto the loader coupler on the pump. As grease transfers, some air may enter the gun which may be vented by the air bleeder valve. The follower plate will minimize air pockets in the bulk grease.
Least environmental impact. No cartridges to discard in landfill.
- Push the loader valve of the grease gun into the coupler on the bulk grease drum.
- Begin pumping the handle of the drum to push grease into the grease gun canister.
- Pump grease into the grease gun canister until the grease gun is full.
- Action the pump of the gun until grease flows out of the coupler.
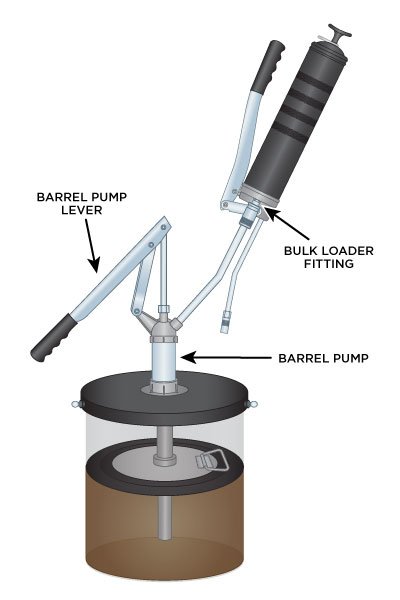
History of Grease Guns
Grease guns (and fittings) were invented in the early 1900s as a remedy for the difficult relubrication process in place to reservice die casting machines. Arthur Gulborg, son of a die-casting manufacturing plant owner, developed a rudimentary lubrication system consisting of a grease fitting, a hose, and a pump screw-type grease gun. This make-shift solution opened the doors to the 100+-year expansion of both the lubrication and the automotive industry.
The following timeline illustrates the general history of how these important components came to evolve within two of the country’s most distinguished lubrication companies:
Alemite® and
Lincoln Industrial® (now an SKF ® subsidiary).
Alemite® Grease Gun History
- 1916: Arthur Gulborg develops the first grease pump to alleviate difficult relubrication processes at the Alemite® Die Casting and Manufacturing plant in Chicago.
- 1918: Gulborg and his father introduce the entire Alemite lubrication system to the U.S. Army, who embraces it as a standard in the summer of the same year.
- 1922: Alemite invents a similar lubrication system with the Button Head design, expanding into civilian industries with heavy-duty applications, like construction.
- 1924: Alemite buys the Allyne-Zerk company, who has at this point invented a much smaller fitting that is gaining in popularity for its efficiency and wide-spread use. Alemite starts selling the Zerk lubrication system, including the P-25 and P-100 air-powered grease gun, to service stations.
- 1920s – 1940s: Alemite lubrication systems continue to advance and develop, making their way into service stations, portable systems for in-field lubrication, the aviation industry, and more.
- 1950s – 1960s: Alemite continues to launch new lubrication system lines, including one of liquid- and corrosion-resistant pumps and others specialized for unique industries.
- 1980s – early 2000s: New grease gun designs become available with increased capacities, more efficient pumping mechanisms, battery-operated options, and customizing characteristics.
- 2010s – present: Grease gun capabilities and designs continue to expand as technology and demand increases.
Lincoln® Industrial Grease Gun History
- 1910: John Lincoln founds Lincoln® Engineering in Cleveland, Ohio.
- 1917: As the automobile industry flourishes, Lincoln takes their mine car lubricator and adapts it for general service station use.
- 1920s: Lincoln invents the Lubrigun®, which manifests in eight different versions and sells prolifically through the decade.
- 1930s: New inventions continued, notably the Centro-Matic® lubrication system.
- 1940s: Lincoln supplies the military with grease guns and fittings, including specialized gas-powered grease guns. Other pump innovations continued to improve and develop.
- 1950s – 1960s: Specialized lubrication lines are enhanced/developed for large-machinery industries, like agriculture and mining.
- 1970s – 1980s: Electric grease guns and the PowerMaster® series are introduced.
- 1990s – early 2000s: Battery-powered and dual-leverage grease guns become available.
- 2010s – present: Existing designs continue to advance and change to meet growing customer needs.
The Bottom Line
Grease guns are an essential component of a lubrication application. Different types of grease guns offer unique benefits conducive to specific application requirements. These tools, along with their accessories, provide you with ways to customize your gun to fit your needs.
Huyett offers a variety of grease guns from trusted brands like Alemite® and Lincoln® that work with our complete line of grease fittings and grease fitting tools & accessories. To learn more about these products, visit our
Grease Fitting FAQ page and our
Lubrication Accessories FAQ page.