- Huyett Marketing Department
- 06/13/2024
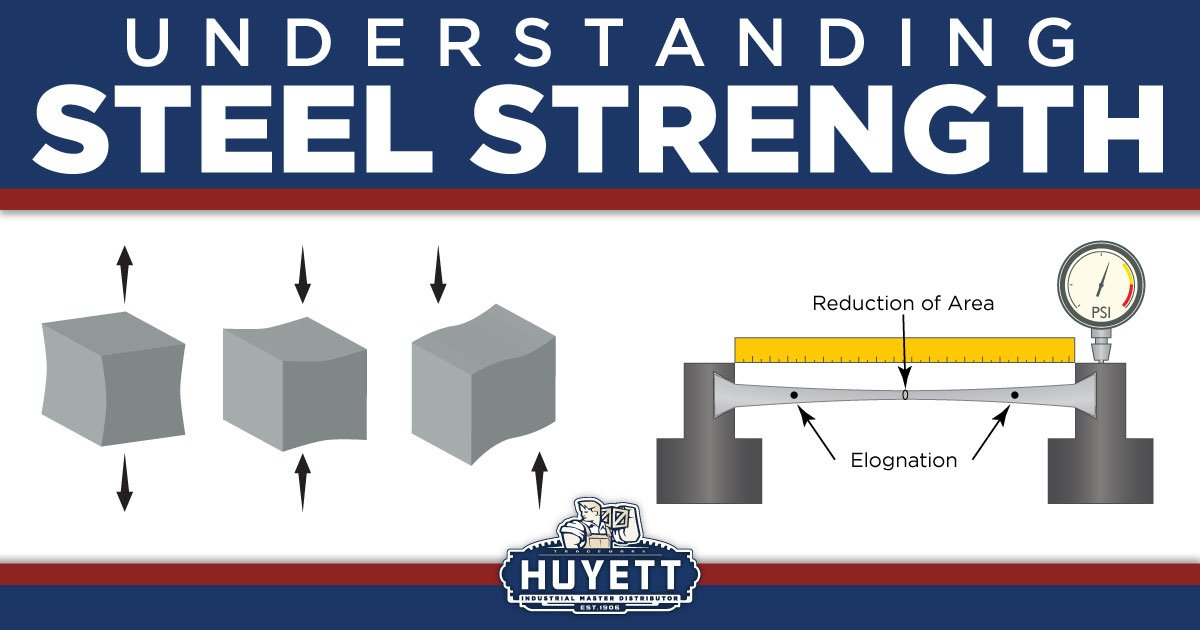
Steel strength is a complex attribute, encompassing several mechanical properties that together determine the material's resistance to external forces and stresses. Understanding it requires evaluating a range of factors, from tensile/yield/shear/compressive strength to environmental conditions. This blog provides an introductory overview of what
steel strength
means –at the end, it covers the basic questions you need to ask when evaluating steel strength for your application.
What Is Steel Strength?
Steel strength is a broad term with no exact measurement. It encompasses several independent mechanical property characteristics of steel and is best described as:
- Steel Strength: The collective result of mechanical behaviors that produce overall resistance to external forces, energies, and stresses before permanent deformation or breaking occurs.
For more information on mechanical properties, visit our
Introduction to Mechanical Properties of Metals.
As you can see, determining steel strength is a challenging task because there are so many variables to evaluate. The complexities arise from several key points:
- It is not exact. Steel strength is the culmination of independent behaviors and their interactions with each other, all of which measure different performance aspects on unique measuring scales.
- The steel composition varies. Different alloying elements alter the mechanical properties, giving steels different strengths.
- Microstructure matters. Grain size, phase distribution, and shape will all affect a material’s ability to resist stresses and forces.
- It isn’t just about the material properties; it also includes its reaction to its environment. Temperature, humidity, corrosion, and loading conditions all have an impact.
That said, a high-level overview of steel strength helps connect the complexities and provide a wholistic understanding of this material component.
Types of Mechanical Steel Strength
At a basic level, overall steel strength can be broken down into four individual strength measurements, which are all calculated as their breaking point when exposed to their respective force or stress. For example, tensile
strength
measures the maximum amount of tensile
stress
a material can handle before giving way and is expressed as a force per unit area.
All four types of strength should be observed both independently and interactively to form a collective observation.
- Tensile Strength: Steel’s ability to resist being pulled apart (also known as ultimate tensile strength).
- Tensile Stress: Pulls materials in opposite directions.
- Yield Strength: The point at which a metal’s elastic behavior gives way to plastic deformation.
- Elasticity: A material’s ability to bounce back to its original shape after experiencing a deforming force.
- Plastic Deformation: Point of permanent deformation (but not breakage).
- Shear Strength: Steel’s ability to resist breaking or slicing along its planes.
- Shear Stress: Force that comes from the side, middle, or opposing directions, enacting itself on just a section of the metal, that could slice or break it.
- Compressive Strength: Steel’s ability to resist being squeezed, compressed, or reduced in size (not as relevant when evaluating steel fasteners).
- Compressive Stress: Force that pushes steel together to shorten it and spread it in a lateral direction.
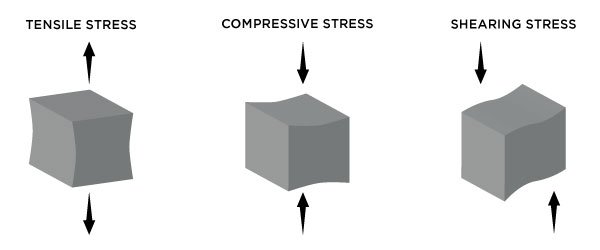
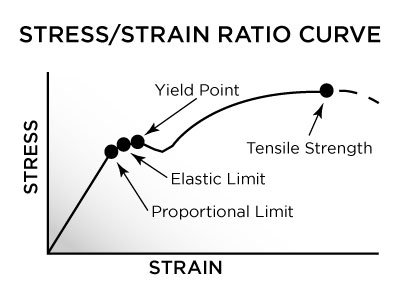
Proportional limit is the point on a stress/strain curve at which it begins to deviate from the straight-line relationship between stress and strain. This is a mathematical point that is not directly observable.
All of these strengths will influence each other. Yield and shear strength will depend on tensile strength, compressive strength depends on yield strength, etc. It is important not to evaluate them in a vacuum. Ultimately, it is helpful to begin with tensile strength, as most other measurements are derived from that.
Other Mechanical Properties That Influence Strength
Considering the nature of tensile, yield, shear, and compressive strength, a metal may be
strong
without being particularly
hard
. This is where hardness and ductility influence the strength of the steel.
Hardness
The relationship between hardness and strength is complex, especially because they measure similar things:
- Strength measures resistance to outside forces and stresses.
- Hardness measures the ability to resist plastic deformation.
While there are many different hardness tests, they are all testing the same thing: how much force does it take to press an object into the material and make a permanent indentation? It would seem that the harder a metal is, the greater resistance it has to an outside force – which indicates strength. In fact, higher tensile and yield strength tends to correlate with more hardness.
However, there are other forces that the steel needs to resist, like breaking. If a steel is particularly hard (like 1095 carbon steel), the material can be brittle enough to easily break, which is the point where strength is overcome. Too much hardness can actually make steel weaker.
Ductility
This is also a hard relationship to quantify, so we’ll start with a definition:
- Ductility: The measure of a metal’s ability to undergo plastic deformation without breaking.
Ductility is measured by two tests:
- Elongation: Measures how far a material stretches before breaking. The test marks two points on the material before it is stretched. Once it is stretched to its breaking point, the points are measured again and the elongation is calculated by the two distances.
- Reduction of Area: Measures how much the area reduces from its starting point to its breaking point. The tests measures the diameter of the material before stretching and after breaking and calculates the difference.
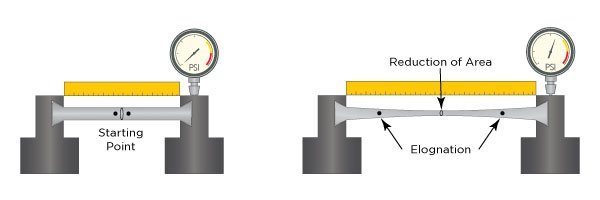
In the definition, we see that there are two types of forces that influence ductility: plastic deformation and breaking or fracturing. Remembering that strength measures the resistance to forces, this can get complicated.
On one hand, ductile steel does not resist the force of plastic deformation well, meaning it likely has low tensile and yield strength. However, once it has deformed, it is flexible and resists fracturing because it is hard to break something that easily bends, likely giving it a lower shear strength.
Machineability
Machineability
refers to the ease with which a material can be cut with minimal chipping or surface finish degradation. A material with high machineability is easily cut with low resistance, while one with a low machineability would require more force, which would likely cause damage.
Good machineability usually correlates to a lower tensile strength – think of the difference between trying to cut putty vs. trying to cut baked clay. The same is true for the relationship with shear strength; if a material is machinable, it is easy to break along its planes.
Toughness
Toughness
is a combination of two properties: ductility and tensile strength. If a material possesses both – that is, if it only bends under a large force and then resists breaking under that force – it is tough. This is particularly helpful when the metal is cracked or worn with fatigue, since the ductility helps prevent small cracks from quickly fracturing.
Clearly, tensile strength contributes to toughness. Since tensile and yield strength often work together, tough steels often have a high yield strength as well. The resistance to breaking under force would also indicate a high shear strength.
Environmental Forces That Lead to Fatigue and Creep
Determining steel strength is not just about the steel itself, but also the environment in which it is operating. You need to examine the relationship between the applied external forces and the resulting deformation and stresses. Repetitive or sustained forces will result in fatigue, creep, or a combination of the two.
The Influence of Force
Forces can occur separately, in combination, or progressively. They are produced by gravity, accelerations and impacts of moving parts, gases and fluids under pressure, the transmission of mechanical power, etc. The timing is also important; force may be static or change so slowly that its maximum value can be treated as if it were static. It may be suddenly applied, as with an impact, or it may have a repetitive or cyclic behavior.
The environment in which forces act on a machine or part also plays a role in the steel’s overall strength. Factors such as high, low, or fluctuating temperatures; the presence of corrosive gases, vapors, liquids, radiation, etc. may have a significant impact on how effectively parts are able to resist stresses.
Fatigue
When steel is subjected to many cycles of stress reversal or fluctuation (variation in magnitude without reversal), failure may occur, even though the maximum stress at any cycle is considerably less than the value at which failure would occur if the stress were constant.
While fatigue is obviously not a property of steel, it heavily influences steel strength. Anything that wears down or damages the material is going to reduce its ability to resist forces, including the forces themselves. Fatigue is essentially the long-term wear and tear of steel combatting stresses.
Modes of Fatigue Failure
Fatigue causes failure in a variety of ways, including those induced by temperatures or corrosive elements. Several modes of fatigue failure are:
Low/High-Cycle Fatigue
This fatigue process covers cyclic loading in two different domains. One domain, known as "high‑cycle fatigue," is characterized by relatively low cyclic loads, strain cycles confined largely to the elastic range, and long lives or a high number of cycles to failure.
The other domain, known as "low‑cycle fatigue" or cyclic strain‑controlled fatigue, has cyclic loads that are relatively high, significant amounts of plastic strain induced during each cycle, and short lives or a low number of cycles to failure.
The transition from low‑ to high‑cycle fatigue behavior occurs in the range from approximately 10,000 to 100,000 cycles. Typical low‑cycle fatigue is defined as failure that occurs in 50,000 cycles or less.
Thermal Fatigue
Cyclic temperature changes in a machine part will produce cyclic stresses if natural thermal expansions and contractions are either wholly or partially constrained. These strains produce fatigue failure just as though they were produced by external mechanical loading.
Corrosion Fatigue
Corrosion fatigue is a mode where cyclic stresses and a corrosion-producing environment combine to initiate and propagate cracks in fewer stress cycles and at lower stress amplitudes than would be required in a more inert environment. The corrosion process forms pits and surface discontinuities that act as stress raisers to accelerate fatigue cracking. The loads may also cause cracking and flaking of the corrosion layer, baring fresh metal to the corrosive environment. Each process accelerates the other, making the cumulative result more serious.
Surface or Contact Fatigue
Surface fatigue failure is usually associated with rolling surfaces in contact with each other and results in pitting, cracking, and spalling, which causes shear stresses to be slightly below the surface. The subsurface shear stresses generate cracks that propagate to the contacting surface, dislodging particles in the process.
Creep Failure
Unlike fatigue failure, creep failure is the result of strain developing from long‑term stress. A solid material can imperceptibly flow or deform when subjected to high temperatures or stresses over a long period. Common examples of creep are the visible distortions in antique glass, the slow movement of glaciers, and the filament pulling apart in household light bulbs.
Combined Creep and Fatigue
In this failure mode, all of the conditions for both creep failure and fatigue failure exist simultaneously. Each process influences the other in producing failure, but this interaction is not well understood.
Application Considerations when Evaluating Steel Strength
When choosing the right steel for your application, there are several questions and factors to consider. Huyett’s Engineering Support Team guides you, the customer, through the consideration process with practical questions so you are better prepared to choose the most appropriate material for your needs.
Here is a list of common questions our team will ask to help you refine your decision, depending on the nature of your application:
- Have you calculated the running load?
- This helps you consider how the material will need to support a load extended over a specific length or area.
- Have you calculated the cyclic load?
- You will need to evaluate if the material needs to support repetitive stresses and their intensity.
- Have you calculated the vibratory load?
- Vibration can wear down a material and affect compressive strength.
- Have you calculated the thrust load?
- The material may need to support a parallel, or axial, force.
- Do mating materials need to have the same hardness?
- This is particularly important to consider for keystock and machine keys.
- Do you have a failure designed into the application?
- You may need to reconsider the material strength if it needs to break before another element in the application.
In general, it is helpful to start by measuring the tensile strength of your steel. Most other important characteristics can be calculated with tensile strength.
The Bottom Line
Steel strength is a complex attribute that involves various mechanical properties determining its resistance to external forces and stresses. It is important to understand how it works so you can evaluate its potential performance in your application; Huyett’s
Engineering Support Team helps you consider different strength factors so you can choose the right material for your needs.
Have more questions?
Reach out to our Inside Sales Team for more information on available materials,
industrial threaded and non-threaded fasteners, and potential customizations.