- Huyett Marketing Department
- 10/10/2019
- Updated: 04/13/2023

Keystock is an important – and perhaps one of the most popular - element of the fastener world. It is used on its own or as the starting point to make other fasteners, particularly in
power transmission applications. But what exactly is keystock, and what type of material is it made from?
Types of Keystock Material
While keystock comes in many different materials, it is mostly available in varying types of steel, aluminum, and brass. Other materials – like Monel® and even nylon – are options but are not as common as the main metals.
Steel
Steel encompasses a broad range of materials including carbon steel, alloy steel, and stainless steel. While carbon is present in all steel, each steel family has a different combination of alloys.
The 4-digit steel numbering system uses the first two numbers to indicate the main alloys and the second two numbers to indicate carbon presence.
Example: 1018 steel (10 = plain carbon; 18 = 0.18% steel)
Carbon Steel
- 1018 : plain carbon; 0.18% carbon
- 1045 : plain carbon; 0.45% carbon
- 1095 : plain carbon; 0.95% carbon
Alloy Steel
- 4140 : chromium/molybdenum; 0.40% carbon
- 8630 : nickel/molybdenum/chromium; 0.30% carbon
Stainless Steel
The stainless steel numbering system only contains 3 numbers, the first of which indicates the stainless steel family and the last two of which indicate the main alloys (not all). These numbers do not communicate carbon presence.
- 303 : austenitic; chromium/nickel/sulfur/phosphorus
- 304 : austenitic; chromium/nickel
- 316 : austenitic; chromium/nickel/molybdenum
- 410 : ferritic & martensitic; chromium/iron/manganese/nickel
- 416 : ferritic & martensitic; chromium/nickel/molybdenum
Aluminum
Aluminum alloys are roughly 1/3 the weight of steel but have great relative strength. The aluminum numbering system, similar to steel's, indicate different elements of the metal's makeup.
The first number indicates the main alloys, the second number indicates alloy modification, and the final two numbers are arbitrarily assigned to trace alloys.
- 6061 : silicon/magnesium; no modification, multiple trace alloys
- 4140 : silicon; modification, multiple trace alloys
Brass
Brass is a subcategory of copper that contains mainly copper and zinc in a roughly 60/40 split. Like most metals, alloys are added to create different grades.
You will see brass grades written as 3 or 5 digits. The industry traditionally gave brass grades arbitrary three-digit names, and the United Number System (UNS) adopted those names and added two digits to create alloy groups.
- 360 : copper/zinc/lead alloy
- 464 : copper/zinc/tin alloy
Monel®
Monel® is a registered trademarked name for a particular group of nickel alloys. They are composed of mostly nickel and copper, with each grade including other trace elements and/or exhibiting different characteristics because of how it was worked.
- 400 : exhibits high corrosion resistance/fair workability
Should I Add Finish to My Keystock?
Adding keystock finish is something to consider depending on the type of elements that the material will be exposed to, as many finishes increase corrosion resistance, hardenability, and aesthetic appeal. Specific finishes, like phosphate conversion coatings, also absorb liquids and improve adhesion. Others, like nickel electroplating, improve the metal's conductivity.
The designer should carefully consider the roll of the material and if finishes would enhance its performance. For a more in-depth look at available material finishes, check out Huyett's
Metal Finishes Introduction.
What is Keystock?
Keystock
is a term that generally refers to
square or
rectangular cold-drawn metal bars that are at least one foot in length and often manufactured to specific tolerances. Other shapes – like
hex,
round, and
step – are available. Keystock should not be confused with machine keys (although the terms are used interchangeably). Machine keys are smaller components cut from keystock.
There are several
fastener industry standards that regulate keystock dimensions, although standard conformance is not necessary. In many cases, if your application requires precision tolerances (whether they must comply with a standard or not), Huyett’s
in-house manufacturing capabilities allows us to cut and/or mill your keystock down to your desired measurements.
However, we do offer keystock that is prefabricated to ANSI B17.1 and several ASTM and DIN standards.
How is Keystock Used?
Keystock is a versatile product with several uses, both in manufacturing and in the field. In manufacturing, keystock is used to create machine keys as an end product.
Machine keys – also known as shaft keys – are essential components in a power transmission application that transmit torque from a rotating shaft to the attached gear. They are used as a “first defense” because they are designed to be the first thing to break, thus preserving the more expensive components in the application.
In the field, keystock is kept on hand to replace broken machine keys on site or for general maintenance.
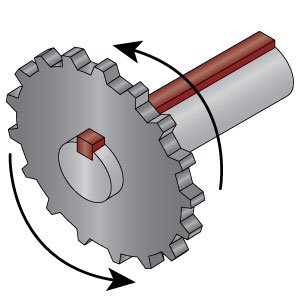
What is Keystock Material?
Keystock (and machine keys) can be made from many types of materials. Typically, keystock is made from metals like carbon steel or stainless steel, aluminum, brass, copper, and Monel®. Each type of keystock metal includes varying material grades that offer different benefits based on their properties.
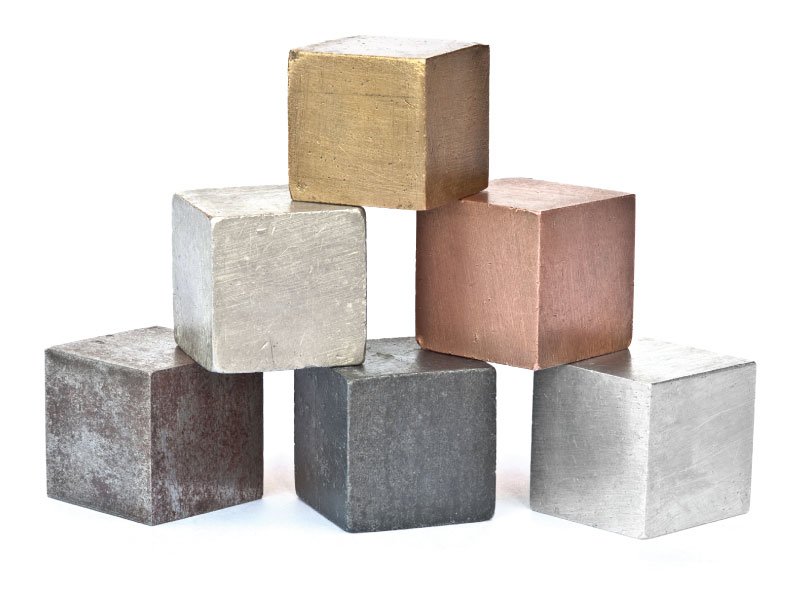
Metal Properties
There are many properties (characteristics) that metal exhibits to communicate how well it will hold up in a given application. To truly understand a metal's functionality, it is important to clarify a few basic terms.
- Strength: A metal’s ability to resist being permanently pulled or bent
- Workability: A metal's ability to be squeezed, stretched, bent, or connected in both its hot and cold forms
- Machinability: A metal’s ability to be cut
- Hardenability: A metal's ability to hold its shape and structure under a compressive force
- Corrosion Resistance: A metal's resistance to natural and manmade corrosive elements
For a more in-depth review of these and other properties, read Huyett’s
Introduction to Mechanical Properties of Metals.
Types of Keystock Material
While keystock comes in many different materials, it is mostly available in varying types of steel, aluminum, and brass. Other materials – like Monel™ and even nylon – are options but are not as common as the main metals. Here, we delve into the different types of keystock material that Huyett offers.
Steel
Steel encompasses a broad range of materials including carbon steel, stainless steel, and alloy steel (each of which are detailed in Huyett’s
Engineering Handbook). While carbon is present in all steel, each steel family has a different combination of alloys (additional metals that add to or enhance the primary metal).
Carbon Steel
Carbon steel, often referred to as plain carbon steel, is a popular choice for keystock, partially because it is an economical choice. It is also good for a wide range of applications in industrial, construction, and automotive industries.
The point of adding carbon to steel is to increase its strength. It does not take much; in fact, the last two digits in steel grade classifications reference the fractional percentage of carbon present in that grade.
For example, 1018 carbon steel tells us that this grade only contains 0.18% carbon. Most steel contains less than 2% carbon; any more gets into the “cast iron” family, where metal is much more brittle. The first two digits refer to the alloy group the metal belongs to; in the 1018 example, 10 refers to plain carbon steel.
Here are three of the most common carbon steel keystock grades:
1018 Carbon Steel
- Strength: Strong, but the least strong of the three grades due to low carbon
- Corrosion Resistance: Does not resist rust and oxygen exposure well
- Hardness: The least hard of the three grades
- Workability: Excellent for welding and cold forming
- Other Information: The most common rolled steel
- Applications: Shaft pins, rods, sprockets, clevis pins, and machine keys
1045 Carbon Steel
- Strength: Stronger than 1018
- Corrosion Resistance: Similar to 1018
- Hardness: Harder than 1018
- Workability: Less workable than 1018, but not impossible
- Other Information: Resistant to wear
- Applications: Similar to 1018
1095 Carbon Steel
- Strength: Strongest of the three grades
- Corrosion Resistance: Similar to 1018
- Hardness: Hardest of the three grades
- Workability: High carbon content makes this very difficult to work
- Other Information: Common choice for cutlery because of its hardness
- Applications: Great for applications that require sharp edges and wear resistance
Stainless Steel
Stainless steel's main elements are iron and chromium. The latter makes the steel "stainless" (highly resistant to rust). From here, stainless steel branches out into five different categories, each with unique alloying properties and designated by a "100 series" classification system:
- Austenitic: 200 & 300 series – Corrosion resistant and durable in a wide range of temperatures
- Martensitic: 400 series – Magnetic, hard, and good for sharp applications like knives
- Ferritic: 400 series – Magnetic, economical, and good for decorative applications
- Duplex: A mix of ferrite and austenite
- Precipitation-Hardening: Heat treatable, magnetic, and corrosion resistant
Some of the most versatile grades of stainless steel are:
303 Stainless Steel
- Strength: Good, but not as strong as 304
- Corrosion Resistance: Decent, but not designed to withstand extreme natural elements
- Hardness: Not as hard as 304
- Workability: Additional sulfur makes 303 extremely machinable, but not very weldable
- Other Information: One of the most workable stainless steels available
- Applications: Good for small fasteners and applications requiring machinability
304 Stainless Steel
- Strength: Decent strength, but not as much as 316
- Corrosion Resistance: Good resistance to natural elements and chemicals
- Hardness: Middle-of-the-road hardness for stainless steel
- Workability: Great for welding and machining
- Other Information: Economical; considered the most versatile stainless steel available
- Applications: Used widely, but particularly in the food industry
316 Stainless Steel
- Strength: Addition of molybdenum makes it slightly stronger than 304
- Corrosion Resistance: Excellent resistance to extreme environments, including saltwater and sub-zero temperatures
- Hardness: Similar to but slightly harder than 304
- Workability: Good machinability and excellent weldability
- Other Information: Known as the marine grade; more expensive than 304, but much better corrosion resistance
- Applications: Good for a wide range of applications, including lab equipment, saltwater applications, and medical equipment
410 Stainless Steel
- Strength: Known for its high strength as a martensitic stainless steel
- Corrosion Resistance: Good resistance to mild natural elements, foods, and acids
- Hardness: High
- Workability: Good for welding and easy to machine if it is annealed or tempered
- Other Information: Economical choice
- Applications: Good for knife blades, fasteners, and spring pins
416 Stainless Steel
- Strength: Decent, but can be increased with heat treatment
- Corrosion Resistance: Good resistance to mild natural elements and food acids
- Hardness: Variable, depending on if it is tempered or hardened
- Workability: Most machinable stainless steel available
- Other Information: Economical choice
- Applications: Good for fasteners, washing machines, and applications with high machining needs
Alloy Steel
Alloy steels still contain carbon, but also consist of about 5% alloying elements including manganese, molybdenum, chromium, vanadium, nickel, and tungsten. Similar to the plain carbon steel classification, alloy steels' four-digit names signify their alloy groups and their fractional percentage of carbon. Two of the most common alloy steel grades are:
4140 Alloy Steel
- Strength: The addition of molybdenum gives it a higher strength than carbon steel
- Corrosion Resistance: Added chromium elevates its resistance to natural elements
- Hardness: Better hardness than carbon steel
- Workability: Highly forgeable, but less cold-workable or weldable than 1018
- Other Information: Used for military clevis pins
- Applications: Extremely versatile and used widely in most industries, including aerospace
8630 Alloy Steel
- Strength: Includes molybdenum and nickel, making it stronger than 4140
- Corrosion Resistance: Similar to 4140
- Hardness: Good hardenability
- Workability: Good ductility, weldability, and machinability
- Other Information: Economical substitute for more expensive alloy steels
- Applications: Keystock, machine keys, and automotive parts
Importance of High Strength Steel
Keystock can be made from steels that possess different strengths. Most carbon and some types of stainless steels can have their strengths increased through heat treatment. A designer must know the calculated or actual strength of the keystock to ensure that it will withstand the operating pressures applied in service. A material that does not have enough strength to withstand the operating pressures will fail.
Aluminum
Aluminum alloys are roughly one-third the weight of steel but have great relative strength. They rival steel in corrosion resistance and heat conductivity and are used in many industries that need light frames, like the aerospace industry.
Similar to the carbon steel classification system, aluminum's four-digit name indicates main alloys, natural or controlled impurities, and trace alloys. In Aluminum 6061, one of the most common grades, 6 indicates that the main alloys are silicon and magnesium, 0 indicates natural impurities, and 61 indicates that there are several trace alloys, including chromium and copper.
Common aluminum alloys include:
6061 Aluminum
- Strength: Decent strength; not as strong as 1018 carbon steel
- Corrosion Resistance: Good resistance to atmospheric conditions; exceptional resistance to ammonia, ammonium hydroxide, and nitric acid
- Hardness: Not as hard as steel
- Workability: Good for forming and welding
- Other Information: Good for electrical conductivity
- Applications: Great general-use aluminum; widely used in architecture and structural applications
4140 Aluminum
- Strength: Good with aluminum expectations
- Corrosion Resistance: Resistant to basic natural elements but can be susceptible because of its copper content
- Hardness: Decent
- Workability: Good for forming and welding
- Other Information: Conducts heat better than steel
- Applications: Good for a wide range of applications, including framework structures, electronic parts, and airplanes
Brass
Brass is a subcategory of copper, which is a pure metal. Brass contains mainly copper and zinc in a roughly 60/40 split. Like most metals, alloys are added to create different grades.
In comparison to steel, while brass is not typically as strong, it is generally more machinable, more corrosion resistant, and more conductive of heat.
You will see the name for a brass grade in a few different forms, most likely as three and five digits. The industry traditionally gave brass grades arbitrary three-digit names, and the United Number System (UNS) adopted those names and added two digits to create alloy groups:
- 20000-29999: Copper/Zinc Alloy – Zinc contributes to strength (brass with over 40% zinc will start to lose malleability)
- 30000-39999: Copper/Zinc/Lead Alloy – Lead increases machinability
- 40000-49999: Copper/Zinc/Tin Alloy – Tin increases corrosion resistance in saltwater
The numbers are only organizational and do not communicate any percentage of alloys.
360 and 464 are two of the most popular brass grades:
360 (36000) Brass
- Strength: Contains roughly 35% zinc; high strength, but still workable
- Corrosion Resistance: Good resistance to natural elements and coolant
- Hardness: High
- Workability: Lead contributes to high machinability
- Applications: Well suited for heavy industry use, including plumbing, and applications that require high machinability
464 (46400) Brass
- Strength: Contains roughly 40% zinc; very high strength brass
- Corrosion Resistance: High, especially in saltwater
- Hardness: High
- Workability: Forgeable and heat workable
- Other Information: Known as "naval brass" for its use in marine environments
- Applications: Good for marine applications, bushings and turnbuckles, and decorative applications
Monel®
Monel® is a registered trademarked name for a particular group of nickel alloys. They are composed of mostly nickel and copper, with each grade including other trace elements. While its workability is not nearly that of steel, the alloy class displays high corrosion and heat resistance.
400 Monel®
- Strength: High
- Corrosion Resistance: High, especially against saltwater and sulfuric and hydrofluoric acid
- Hardness: Hardens during cold working
- Workability: Fair, but requires specific forging and welding techniques
- Other Information: Keeps its corrosion and strength properties at over 700°F
- Applications: Great for marine applications, chemical environments, and extreme temperatures
Keystock Metal Tolerance: Moltrup®
Moltrup® can be a confusing term. It does not refer to a specific type of material; instead, it references a tolerance quality introduced by the Moltrup Steel Products Co. in Pennsylvania. This tolerance meets the ASME B17.1 Class 2 fit, which is a tight keystock and key seat fit.
1018, 1045, and 8630 steel grades are some of the metals that can conform to the Moltrup quality.
Other Keystock Material: Nylon
In addition to metal, nylon keystock is also available. While it is not nearly as strong as steel, it is cost efficient, flexible, durable, and resistant to chemicals.
Nylon comes in several grades, but 6/6 offers a range of characteristics that make it a good choice for keystock:
6/6 Nylon
- Strength: About 1/10th the strength of low carbon steel
- Corrosion Resistance: Good resistance to oil, gas, and chemicals
- Hardness: Good
- Workability: High
- Other Information: Electrically insulating
- Applications: Can be an economical substitute for metal washers and bearings and is used widely in many industries, particularly the medical industry
Choosing the Right Keystock Material
Keystock materials should be chosen based on the operating environment. You should carefully consider the loads that will be applied to the material and what type of atmosphere it will be subjected to in service.
Carbon steel provides very good strength and can be altered through heat treatment to provide a higher degree of strength or wear resistance. Alternatively, austenitic (300 series) stainless steel keystock material should be used where the material will be exposed to highly corrosive environments, and martensitic stainless-steel keystock material should be used when higher strength material is required and exposed to mildly corrosive environments.
Where brass is concerned, lead alloys offer high machinability and are often used in plumbing, where tin alloys are good options for marine applications. Nickel alloys offer corrosion resistance to extreme elements, and nylon is well suited for economical applications that require resistance to chemicals.
In addition to operating environments, you should consider cost and availability when choosing keystock material. One of the many
benefits of becoming a Huyett distributor is having your material’s real-time price and stock status immediately available at your fingertips through our online experience.
Should I Add Finish to My Keystock?
Adding keystock finish is something to consider depending on the type of elements that the material will exposed to, as many finishes increase corrosion resistance, hardenability, and aesthetic appeal. Specific finishes, like phosphate conversion coatings, also absorb liquids and improves adhesion. Others, like nickel electroplating, improve the material’s conductivity.
The designer should carefully consider the role of the material and if finishes would enhance its performance. For a more in-depth look at available material finishes, check out Huyett’s
Metal Finishes Introduction.
The Bottom Line
Keystock is widely used to make
machine keys for power transmission applications. Since they are used to protect the expensive components within the application, it is important to understand what keystock material is available and how to choose the right one.
Huyett stocks hex, rectangle, round, square, and step keystock in multiple materials with a variety of optional finishes. To learn more about our options, browse our
Keystock catalog or
our keystock selection, or
contact our Sales Team for more information.