
Where to buy rivet nuts:
Rivet nuts can be purchased from Huyett online or by phone! Huyett is a proud master distributor of AVK Industrial Products and Sherex Fastening Solutions rivet nuts. We pride ourselves in having one of the widest selections of blind rivet nuts in the industry, which means you spend less time trying to find the right parts for your unique needs. If you don't see what you are looking for, contact us to speak with our knowledgeable and friendly sales team!
What is a rivet nut?
A rivet nut, also known as a blind threaded insert, is a one‑piece internally threaded fastener with an engineered body that compresses when installed, thus securing the fastener in place. They are commonly installed in applications with blind fastening requirements, however, they have become more frequently utilized in high production volume environments due to simple installation and economical costs. Rivet nuts can be installed on pre‑painted components without distorting the base material and are a suitable replacement for weld nuts, eliminating weld spatter and toxic fumes.
What is a blind insert or fastener?
A blind insert, or blind threaded insert, is another term for the more commonly known rivet nut. For more details on blind inserts, check out our rivet nut features section!
What are the common types of rivet nuts?
The most common rivet nut styles include knurled and hex open ended bodies. Both styles provide spinout resistance when torque is applied from tightening or loosening threaded fasteners. The open ended body allows for more flexibility by not limiting the length of the fastener that can be used.
How do rivet nuts work?
Rivet nuts, also called blind thread inserts, are used to provide a strong threaded anchor point in thin or brittle substrates that are not suited for tapping. When installed, the body of the nut collapses, creating a bulge that pinches the substrate between it and the nut flange.
What kind of rivet nut do I need?
Some considerations should be taken into account when choosing the right rivet nut for your application. While body style is often the most important, there are other attributes that should be factored in the decision making process. Take a look at our guide to assist you in making the right choice for your needs!
Attribute
| Description
| Styles
|
---|---|---|
Body Style
| Different styles and duties accommodate installation and production needs. Closed end rivets provide a contamination barrier.
| Round: Smooth or Knurled
Hexagonal: Full Hex or Semi-Hex Slotted: Straight or Pre-Bulbed Swaged: Smooth or Diamond Knurled Floating: Standard or Short Stud: Male Threaded Stud |
Material/Finish
| Multiple options available to provide strength and corrosion resistance in your application.
| Steel, Stainless Steel, Aluminum, Zinc Clear, Zinc Yellow, Passivated, or Cadmium
|
Flange/Head Size
| The head/flange provides push out resistance based on application need.
| Large flange or Small flange
|
Thread Size
| The most common thread sizes available to add strong threads in thin materials.
| Inch or Metric
|
Grip Range
| Get the proper fit on any material with multiple grip ranges.
| Common thicknesses available for each application.
|
Overall Length
| Various lengths available to fit your specific application need.
| Common lengths available for each application.
|
Rivet Nut Body Style Features:
There are numerous variations of rivet nut bodies to choose from. We've compiled a list of the most popular styles offered by Huyett!
- Round Rivet Nuts: Round bodied rivet nuts feature either a smooth or knurled surface. While both provide minimal spinout resistance, a knurled surface provides additional torque resistance.
- Hexagonal Rivet Nuts: Hexagonal rivet nuts provide the ultimate spinout resistance. Full hexagonal, or full hex, rivet nuts are designed for heavy duty applications. For lighter duty needs, half hexagonal rivet nuts are suitable. Hexagonal nuts are recommended if hex shaped holes can be produced.
- Slotted Rivet Nuts: Slotted rivet nuts feature a round slotted body and are available with a straight or pre‑bulbed shank. Both varieties offer a large grip range for variable material thicknesses, as well as a large footprint for increased pullout resistance. Pre‑bulbed shanks provide some spinout resistance.
- Swaged Rivet Nuts: Swaged rivet nuts provide strong threads in thicker sheet materials, tubing, or blind holes requiring reduced clearance. The unique swaging design allows the threaded portion of the rivet nut to separate and pull up into the shank, creating a bulge that wedges the rivet nut firmly into the work piece.
- Floating Rivet Nuts: Floating rivet nuts can compensate for misalignment caused by tolerance stack up or servicing of joint. Body lengths are often designated as standard or short to accommodate different substrate thicknesses.
- Rivet Nut Studs: Rivet nut studs, or studded rivet nuts, are a two‑piece fastener composed of a rivet nut body and a male threaded stud. These are suitable for attaching thin material in blind applications and a great alternative to clinch or weld studs.
How to install rivet nuts:
Rivet nuts, or blind threaded inserts, can be installed using simple or specialized rivet nut tools. The most common rivet nut tools are manual hand tools, pneumatic spin-spin rivet guns, and hydro-pneumatic spin-pull rivet guns.
Installing a rivet nut manually by hand
Hand installation of rivet nuts can be accomplished using a variety of manually powered hand tools. The most common types are ratchet, lever, and hand. To use, simply thread the insert onto the end of the tool and action the tool until the side wall of the rivet nut has collapsed, securely pinching the parent material. Manual hand installation is great for small production quantities and prototyping.
Installing a rivet nut with Pneumatic Tools
Pneumatic, or spin‑spin, rivet nut tools are air powered pneumatic tools that feature either a pistol grip, right angle, and inline form factor. The rivet nut is threaded onto the mandrel which is spun inward, collapsing the walls of the rivet nut. Once the walls are fully collapsed, the tool reverses and separates from the installed fastener.
Installing a rivet nut with hydro‑pneumatic tools
Hydro‑pneumatic, or spin‑pull, rivet nut tools use a combination of compressed air and hydraulics to install rivet nuts. To install a rivet nut using a spin‑pull rivet nut tool, simply thread the nut onto the end of the tool's mandrel. After the fastener is inserted into the work piece, the mandrel retracts, pulling the threads of the rivet nut into the work piece. Once the rivet nut is installed, the tool unthreads from the fastener.
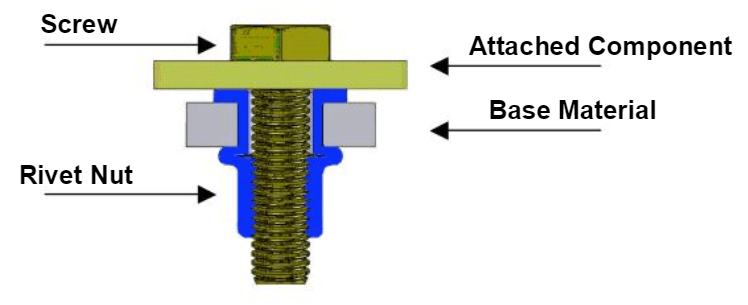

How does a rivet nut gun work?
Rivet nut guns have three distinct methods for installing blind thread inserts.
- Spin‑spin
- Spin‑pull to pressure
- Spin‑pull to stroke
Spin‑spin rivet nut guns:
Spin spin rivet nut guns use air pressure to spin the chuck, or mandrel, of the gun. As the mandrel spins, it draws the body of the insert in. This action collapses the wall of the rivet nut, securing it to the desired substrate. Once the threaded insert is installed, the mandrel reverses its rotation to separate from the fastener. This style of rivet nut gun requires awareness from the operator as to not over‑tighten the rivet nut.
Spin‑pull to pressure rivet nut guns:
Spin‑pull to pressure rivet nut guns install the fastener based on a pre‑set pressure determined by the operator. The rivet nut is threaded onto the mandrel, which retracts, pulling the threads of the fastener into the parent material until a pre‑determined pressure is achieved. Pull to pressure installation is ideal for parts with variable material thickness.
Spin‑pull to stroke rivet nut guns:
Spin‑pull to stroke rivet nut guns install the fastener based on a pre‑set stroke length determined by the operator. The rivet nut is threaded onto the mandrel, which retracts, pulling the threads of the fastener into the parent material until a pre‑determined stroke is reached. Pull to stroke installation is ideal for parts with a uniform material thickness.
What materials are best for use with rivet nuts?
Rivet nuts work with a wide range of materials including carbon fiber, plastic, fiberglass, steel, and aluminum. They work best in thin walled applications where tapped holes are not feasible. Rivet nuts work by clamping to the mating material when the body is compressed to create a threaded attachment point where traditional threaded holes cannot be formed.
How strong are rivet nuts?
Rivet nuts are incredibly strong, boasting similar resistance to stresses as bolt and nut combinations. Testing should be completed when identifying solutions where specific load tolerances must be met. For additional information, or questions regarding a specific application, contact our knowledgeable, friendly sales team.
How to remove rivet nuts:
Grinding method
- Thread a long bolt into the rivet nut to act as a holding point.
- Fit a dremel or angle grinder with a grinding wheel.
- Carefully grind away the head of the rivet nut without damaging the mating component.
- Holding on to the bolt, push the remainder of the rivet nut further into the hole to expose the flanged sides.
- Using a pair of needle nose pliers, manipulate the flanged ends so that the body of the rivet nut can pass through the hole for removal.
Drilling method
- Use a drill bit slightly larger than the threaded hole of the rivet nut.
- Drill through the rivet nut to separate the head of the rivet nut from the body.
- Continue to step up the drill bit size until the rivet nut separates.