
What is the difference between a shim, spacer, or washer?
Shims, spacers, and washers are all similar in appearance and design. However, each possess unique characteristics that make them suitable for specific applications.
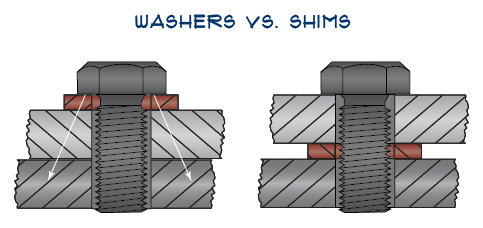
- Shims refer to a broad class of specialty flat washers used for positioning and spacing. They have the same visual appearance of a common flat washer but are often made from non‑ferrous materials. Shims are crafted using precise materials and production techniques to produce smooth corners, flat edges, and a parallel face. They maintain very flat surfaces and consistent thicknesses across the part.
- Spacers, also referred to as a stand‑off, is a fixed size component designed to provide a pre‑determined distance between two adjoining parts. While shims typically feature a thin profile, spacers are designed with a much wider range of thicknesses from several inches to several feet depending on application requirements. Spacers can also be purposed as sleeves, bushings, axles, or pins.
- Washers are a common fastening component that is stamped from thin metal sheeting. While they can be used for spacing, they perform best when used in tandem with conventional threaded fasteners to spread loads produced by fasteners from tightening or to reduce unwanted loosening. Washers are often crafted with less precision than shims or spacers and can possess curves, splits, or tangs as is common with Belleville, curved, and lock washers.
What is a compression limiter?
Compression limiters are a non‑threaded, tubular insert used to provide a maintain joint integrity for applications that could be damaged by compressive loads. These spacers are ideal for bolted joints in plastic assemblies where tightening forces can compromise the integrity of joining parts. Compression limiters are manufactured in a wide range of types including split seam, molded‑in, knurled, and flange headed.
What are slotted shims used for?
Slotted shims, sometimes referred to as horseshoe shims or slotted motor shims, are an efficient way to solve alignment and leveling problems on already assembled components. They are installed by sliding into the open space between the assembled components. The slot of the shim is fitted against the bolt or pin that holds the assembly together. Slotted shims are commonly used to align body panels on vehicles or drive trains on some power transmission assemblies.
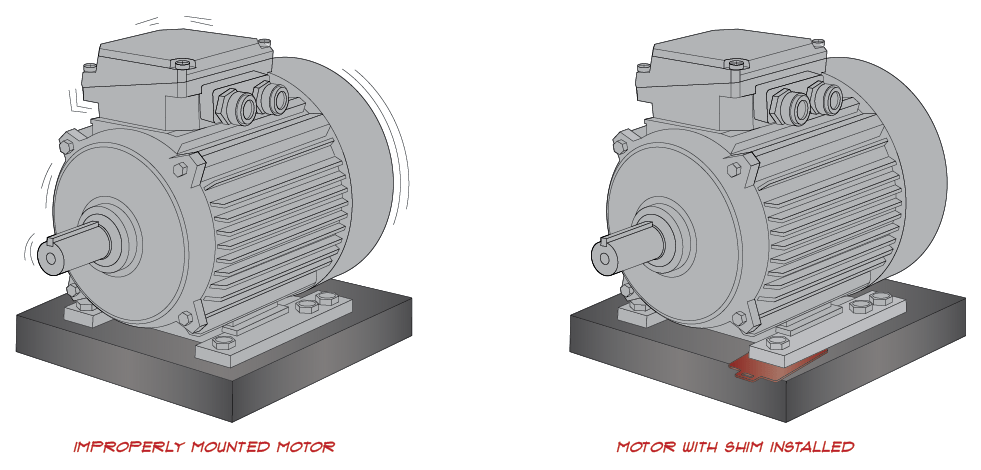
How to use variable shims:
Variable shims, also known as lengthening or shortening shims, are used to increase or decrease the effective length of a shoulder screw or stripper bolt. Lengthening shims are designed to be positioned over the threads of a given bolt to increase the effective length of the bolt's shank. Shortening shims, however, are designed to be seated under the bolt's head to decrease the effective length of its shank.
What are the best practices when using shims?
- Do not use more than 4 shims per application. Too many shims can produce slippage and increase risk of contamination.
- When using multiple shims, thinner shims should be positioned between thicker shims.
- Never shim more than an overall elevation of .150"
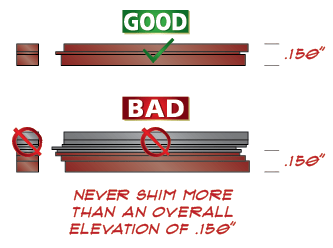
How is tool wrap used?
Tool wrap is most often cut and folded into an envelope that protects material by preventing contamination during the heat treating process of tool making.
How to use tool wrap for heat treating:
- Using a pair of heavy duty scissors or tin snips, cut a piece of tool wrap that is roughly two and a half times the size of the tool being wrapped.
- Fold the tool wrap in half using a hammer or roller to create a clean, crisp fold.
- Fold over one end of the wrap onto itself twice. Create a thick, air tight seal by pressing each fold with a hammer or roller.
- Repeat step three for the long end of the wrap. This should leave one short end open for inserting the tool needing treated.
- Insert the tool through the remaining opening of the envelope.
- Seal the remaining opening of the envelope by repeating Step #3.
How to use a feeler gauge:
- Refer to your component's manufacture's or engineer's guidelines for clearance tolerances required.
- Fan out the leaves of the gauge to display the different sizes.
- Select the "leaf" from the gauge that falls within the tolerance range specified or looks to closely fit the gap being measured.
- Put the remaining leaves back so they do not create obstructions while measuring.
- Insert the selected leaf into the void between the two components being checked. There should be light contact, or drag, between the surfaces of the components and the feeler gauge. If the leaf does not fit into the void, do not force it. This means that the clearance is too tight. If the gauge moves too freely, the tolerances are too great.
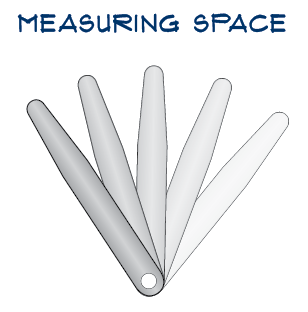
What are feeler gauges used for?
Feeler gauges are used to precisely measure clearance between mechanical components in tight tolerance assemblies such as internal combustion engines. Their use is often necessary during component set‑up for routine maintenance and repair.